शीट मेटल प्रेसिंग क्या हैं? |What is sheet metal pressing in Hindi?
स्टील , तांबा , पीतल , माईल्ड स्टील , टिन , जी आई , एल्युमिनियम जैसी धातुओं की शीट के टुकड़े या कॉईल एक विशेष प्रकार की डाई में प्रेस मशीन द्वारा उच्च दबाव (pressure) के ज़रिये सामान्य तापमान पर दबाकर शीट को पार्ट्स में परिवर्तित करने की प्रक्रिया को शीट मेटल प्रेसींग कहा जाता हैं
इस प्रक्रिया की मुख्य विशेषताएं यह हैं :
- कच्चा माल (raw materials) कोई न कोई धातु – शीट या कॉईल के रूप में – होती हैं . हालाँकि , कई बार कच्चा माल पाईप, ट्यूब , एल्युमिनियम के extruded प्रोफाइल , एम एस के ऐंगल या चैनल भी होतें हैं .
- प्रक्रिया सामान्य तापमान पर सम्पन्न होती हैं , शीट या कॉईल को उच्च तापमान पर दबाने की आवश्यकता नहीं पड़ती
- डाई जो होती हैं वह part को समर्पित होती हैं , यानि की डाई जिस पार्ट के लिए बनी होती हैं वही पार्ट उसमें बन सकता हैं, कोई अन्य पार्ट नहीं बन सकता .
- उच्च दबाव प्रेस मशीन द्वारा बनाया जाता हैं . प्रेस मशीन mechanical , हाइड्रॉलिक , नूमैटिक या हस्तचालित (hand press) हो सकती हैं
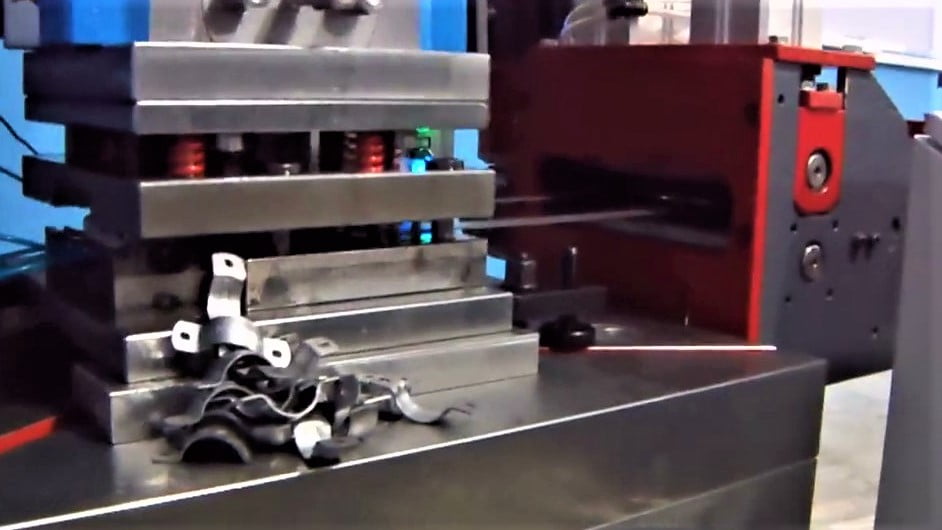
शीट मेटल प्रेसींग प्रक्रिया में प्रोग्रेसिव डाई , कॉईल फीडर एवं डिकॉईलर के इस्तेमाल से बनते हुए सैडल
पश्चिमी देशों में इस प्रक्रिया को शीट मेटल स्टेमपिंग के नाम से जाना जाता हैं और इससे बने पार्ट्स को स्टेमपिंग या stamped parts कहा जाता हैं . दुनिया के अन्य हिस्सों में पार्ट्स को प्रेस पार्ट्स एवं प्रेस कम्पोनन्ट कहा जाता हैं .
शीट मेटल प्रेसींग प्रक्रिया से कौनसे पार्ट्स बनाए जाते हैं ?
आसपास में नजर दौड़ाई और कोई प्रेस पार्ट न दिखा ऐसा हो नहीं सकता !
रसोईघर में नजर घुमाईए ज़रा . भगोने , पतेले , चाकू -छुरी , फोर्क , चम्मच , कैन ओपनर और कई प्रकारके cookware दिखेंगे . ये सारे प्रेसींग से बनाए गए हैं .
प्रेस पार्ट्स ही हैं जिनकी वजह से आज कार की कीमतें एक औसत इन्सान की खरीदशक्ति के दायरे में आ चुकी हैं . एक कार में हजारों प्रेसींग से बने पुर्जे होते हैं जैसे की बोनेट , डिक्की , छत , वाईपर , दरवाज़े , टंकी , नंबर प्लेट आदि .
फ्रीज़ और वाशिंग मशीन लगभग पूरे ही प्रेस पार्ट्स से बने हैं .
किसी भी कमरे में नजर घुमाईए – ट्यूबलाइट की पट्टी हैं वो प्रेस पार्ट हैं. लाइट बल्ब का निचला हिस्सा प्रेस पार्ट हैं . कंप्युटर , आडिओ सिस्टम , टी वी जैसे उत्पादों की अंदरूनी फ्रेम प्रेस पार्ट्स से बनी होती हैं .
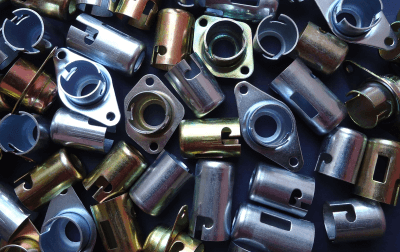
An assortment of automotive bulb holders
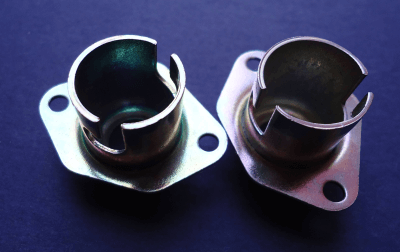
Automotive turn signal bulb holder assemblies
इलेक्ट्रिक मोटर के दोनों सिरों पर लगे कवर , भीतर की stator core , armature , इलेक्ट्रिकल contacts आदि प्रेसींग से बने प्रेस पार्ट्स ही हैं . मोटर को ऑन-ऑफ करने के लिए जो स्टार्टर होता हैं उसका बाहरी डिब्बा एवं कवर , भीतर के रीले के कई पार्ट्स प्रेसींग से बने होते हैं .
आपके शरीर पर भी बहुत सारे प्रेस पार्ट्स देखने को मिल जाएंगे – वो जो घड़ी हाथ में पहनी हैं उसके अंदर कई प्रेस पार्ट्स हैं ; जेब में पेन हैं उसकी क्लिप; चश्मा पहना हैं उसकी फ्रेम; पैरों के जूतों की lace जिसमें बांधते हैं वह eyelets; पतलून में लगी स्टेनलेस स्टील की क्लिपें ये सारी चीजें प्रेसींग से बनी हैं .
वर्तमान में हमारा जो जीवनस्तर हैं उसे बनाने में प्रेस पार्ट्स की बड़ी अहम भूमिका रही हैं .
शीट मेटल प्रेसिंग प्रक्रिया का उपयोग कहाँ किया जाता हैं ?
बड़े स्तर पर शीट मेटल प्रेसींग प्रक्रिया जिन उद्योगों में प्रयुक्त की जाती हैं ऐसे कुछ उल्लेखनीय उद्योग इस प्रकार हैं :
- आटोमोबाइल उद्योग (कार , मोटरसाइकिल , ट्रक , ट्रैक्टर आदि )
- विद्युत उपकरण उद्योग (मोटर , स्टार्टर , स्विचगियर, ट्यूबलाइट एवं बल्ब , स्टैबलाइज़र , इंवर्टर आदि )
- White Goods उद्योग ( फ्रिज , वाशिंग मशीन , माइक्रोवेव अवन , एयर कन्डिशनर , टी वी आदि )
- कंप्युटर हार्डवेयर उद्योग (कंप्युटर केस , हार्डडिस्क , यूएसबी , फ्रेम आदि )
- चिकित्सा उपकरण उद्योग (कैटस्कैन मशीन , सर्जरी औज़ार , फर्निचर आदि)
- बर्तन एवं कुकवेयर उद्योग
- रक्षा उपकरण उद्योग
- एरोस्पैस उद्योग
ऐतिहासिक रूप से आटोमोबाइल उद्योग प्रेसींग प्रक्रिया प्रयुक्त करने में सबसे आगे रहा हैं . इसीलिए इस प्रेसींग के क्षेत्र में ज्यादातर नए आइडियाज़ आटोमोबाइल उद्योग से ही आते रहे हैं .
शीट मेटल प्रेसिंग ही क्यों ?
शीट मेटल प्रेसींग को समस्त मैन्यफैक्चरिंग सेक्टर का सबसे बड़ा ‘खिलाड़ी’ यूँ ही नहीं कहा जाता ! कुछ ठोस कारण हैं इसके पीछे .
पहली बात तो ये की अन्य मैन्यफैक्चरिंग टेक्नॉलजी से यह बहुत अधिक तेज हैं . Forging , machining , कास्टिंग , पाउडर मेटलर्जी , extrusion जैसी अन्य प्रक्रियाएं गति के मामले में इसके सामने कहीं नहीं ठहरती – automation के बगैर ही !
दूसरी बात ये की यह automation के लिए बहुत अनुकूल हैं .
तीसरी बात ये की प्रेसींग किए हुए पहले पार्ट और 10,000 वे पार्ट के dimensions में बहुत कम फर्क होता हैं . यानि की dimensions की पुनरावृत्ति अन्य प्रक्रियाओं की अपेक्षा ज्यादा होती हैं . dimensions को अच्छी तरह नियंत्रित कर सकते हैं .
इन सभी अच्छाईयों के फलस्वरूप प्रेसींग प्रक्रिया निम्न लाभ अर्जित करती हैं :
- विशाल उत्पादन मात्रा
- सटीक dimensions की पुनरावृत्ति
- कम उत्पादन लागत
इन्ही लाभों की वजह से प्रेसींग पहली वरीयता प्राप्त प्रक्रिया बन जाती हैं .
शीट मेटल प्रेसिंग प्रक्रिया के विभिन्न चरण कौनसे हैं ?
प्रोग्रेसिव डाई वाली प्रेसींग को छोड़ दे तो ऐसा कम ही होता हैं की किसी पार्ट को प्रेसींग से बनाने हेतु एक से अधिक चरणों की आवश्यकता न पड़े . और जब भी एक से अधिक प्रेस ऑपरेशन करना जरूरी हो जाता हैं तब blanking ही पहला ऑपरेशन होता हैं जिसमे पार्ट शीट से जुदा हो जाता हैं . इसके ठीक विपरीत , प्रोग्रेसिव डाई प्रेसींग में एक ही स्ट्रोक में सारे ऑपरेशन सम्पन्न हो जाते हैं और सबसे आखिरी स्टेशन पर पार्ट शीट से अलग हो कर नीचे गिर जाता हैं.
पहले चरण में शीट /कॉईल/पट्टियों से पार्ट blanking डाई की सहायता से काटा जाता हैं . इस ऑपरेशन को blanking कहा जाता हैं और पार्ट्स को blanks कहा जाता हैं . blanking सबसे पहले इसलिए किया जाता हैं की blanks का handling शीट /कॉईल/पट्टियों के handling से आसान होता हैं .
इसके बाद प्रेसींग के कौनसे चरण प्रयुक्त होंगे यह पार्ट की ज्यामिति (geometry) कैसी हैं और पार्ट के dimension टालरन्स (tolerance) क्या हैं इन चीजों पर निर्भर करता हैं .
विभिन्न परिस्थितियाँ हो सकती हैं , हर मामले में चरणों की शृंखला भिन्न होगी .
- यदि गोल वाशर बनाना हो तो पहले blanking और उसके पश्चात center hole के लिए piercing करना होगा
- यदि कोई डिशनुमा पार्ट जिसमे सेंटर hole हो तो पहले blanking , बाद में forming और अंत में piercing करना होगा
- यदि इसी पार्ट में कहीं उभरा हुआ कोई feature हैं तो forming और piercing के बीच एक embossing ऑपरेशन का प्रावधान करना होगा
- यदि कटोरिनुमा पार्ट बनाना हो तो पहले blanking, बाद में draw उसके बाद में trimming करना होगा
इससे यह स्पष्ट होता हैं की अलग अलग परिस्थितियों में विभिन्न ऑपरेशन भिन्न भिन्न क्रम में करने होते हैं . जाहीर हैं की ऐसा कोई नियम नहीं बनाया जा सकता जो हर मामले में लागू होता हो .
शीट मेटल प्रेसींग प्रक्रिया के विभिन्न प्रकार कौनसे हैं ?
कई विशेषज्ञों की राय में प्रेसींग प्रक्रिया के चार प्रकार हैं . प्रेसींग के दौरान दो ऑपरेशन के बीच पार्ट्स किस तरह से handle किया जाता हैं यह ध्यान में रख कर यह प्रकार बनाए गए हैं .
पारंपरिक प्रेसींग प्रक्रिया
इस प्रक्रिया में प्रत्येक (कभी कभी दो) ऑपरेशन के लिए एक प्रेस और एक डाई की आवश्यकता होती हैं . शीट में से काटी गई पट्टियाँ डाई में हाथों से डाल कर आगे की और सरकाई जाती हैं .
जैसे जैसे पहले प्रेस पर पहला ऑपरेशन सम्पन्न होता है वैसे वैसे वे पार्ट्स शृंखला के दूसरे ऑपरेशन की डाई जिस प्रेस पर लगी हो उस प्रेस पर पहुँचाए जाते हैं . वहाँ दूसरा ऑपरेशन सम्पन्न होता हैं और इसी क्रम में प्रक्रिया आगे बढ़ती रहती हैं जब तक की आखिरी ऑपरेशन सम्पन्न न हो जाए .
ऐसा कई बार होता हैं की ऑपरेशन ज्यादा और प्रेस कम हो . तब एक ही प्रेस बारी बारी से विभिन्न ऑपरेशन सम्पन्न करती हैं . इस सूरत में पूरी तरह सम्पन्न पार्ट (finished part) पाने में विलंब होता हैं .
इस प्रक्रिया में जो डाईयाँ इस्तेमाल होती हैं वो ज्यादा महंगी नहीं होती . परंतु पूरी तरह सम्पन्न पार्ट पाने में विलंब होने के कारण उत्पादन क्षमता बढ़ाने हेतु ज्यादा डाईयाँ एवं प्रेस प्रयुक्त करने पड़ते हैं . यानि की लागत बढ़ जाती हैं .
प्रोग्रेसिव डाई प्रेसींग प्रक्रिया
प्रोग्रेसिव डाई प्रेसींग प्रक्रिया में एक ही डाई और एक प्रेस का इस्तेमाल होता हैं . डाई जटिल और महंगी होती हैं क्योंकि एक ही डाई में सारे ऑपरेशन करने हेतु विभिन्न स्टेशन होते हैं और इसमें बहुत अधिक सटीकता (accuracy) की आवश्यकता रहती हैं .
कच्चा माल कॉईल के रूप मे होता हैं . एक डीकायलर (decoiler) मशीन होती हैं जो कॉईल को घुमाती हैं. कॉईल आगे फीडर में से होते हुए डाई के विभिन्न स्टेशन से गुजरती हैं. प्रत्येक स्टेशन पर एक ऑपरेशन एक ही समय पर सम्पन्न होता हैं .
Blanking को छोड़ कर अन्य सारे ऑपरेशन पहले किए जाते हैं जिसकी वजह से पार्ट कॉईल से जुदा नहीं होता . पार्ट कॉईल के साथ आगे blanking स्टेशन की ओर बढ़ता रहता हैं . आखिरी blanking स्टेशन पर पार्ट कॉईल से जुदा हो कर नीचे गिरता हैं .
इस तरह प्रेस के प्रत्येक स्ट्रोक के साथ एक पूर्णतया सम्पन्न पार्ट बन जाता हैं . यह प्रक्रिया पारंपरिक प्रक्रिया से 2-3 गुना तेज होती हैं और इसमे ऑपरेटर की आवश्यकता भी नहीं रहती . इसलिए इस प्रक्रिया से बने पार्ट्स पारंपरिक प्रक्रिया से बहुत अधिक सस्ते होते हैं .
परन्तु एक ही समय पर सारे ऑपरेशन होने की वजह से और प्रोग्रसिव डाई लंबाई में बड़ी होने की वजह से इस प्रक्रिया में बड़े साइज़ (tonnage) के प्रेस की जरूरत होगी . यानि की प्रेस भी बड़ी और डाई भी बड़ी रहेगी .
ट्रान्सफ़र डाई प्रेसींग प्रक्रिया
ट्रान्सफ़र डाई प्रेसींग प्रक्रिया कई मायनों में पारंपरिक प्रेसींग जैसी होती हैं . फर्क सिर्फ यह होता हैं की पार्ट्स की हैंडिलिंग आटोमेशन (automation) की सहायता से की जाती हैं .
प्रेस मशीनें अगल बगल में एक दूसरे के नजदीक लगाई जाती हैं ताकि पार्ट्स के हैंडिलिंग में सुविधा हो . प्रत्येक प्रेस पर एक डाई लगी होती हैं . पहली प्रेस पर blanking हो जाने के बाद वह blank बगल की डाई में निर्धारित जगह पर आटोमेशन (automation) की सहायता से ले जा कर वहाँ रख दी जाती हैं .
यहाँ दूसरे चरण का ऑपरेशन सम्पन्न होता है और उसी समय पहली प्रेस पर एक और blank बन जाती हैं . इसके बाद यह blank और दूसरे चरण का पार्ट पुनः आटोमेशन (automation) की सहायता से एक ऑपरेशन आगे बढ़ते हैं .
अंततः आखिरी प्रेस पर पार्ट पूरी तरह बन जाता हैं और आटोमेशन (automation) प्रणाली उसे धातु या प्लास्टिक से बने एक बक्से (bin) में डाल देती हैं . यानि की जीतने ऑपरेशन होंगे उतनी प्रेस -डाई होगी . पार्ट्स निरंतर बनते रहते हैं.
यह प्रक्रिया पूरी तरह से स्वचालित हैं और इस कारण पारंपरिक प्रक्रिया से ज्यादा उत्पादन देती हैं , ऑपरेटर से संबंधित खर्च भी नहीं लगता . परन्तु लागत ज्यादा बैठती हैं .
यह प्रक्रिया उन परिस्थितियों में फायदेमंद साबित होती हैं जहाँ बड़े साईज़ के पार्ट्स बनाने हों . पार्ट्स बड़ी साईज़ के हो तो पारंपरिक प्रक्रिया में हैंडिलिंग cost ज्यादा आती हैं . बड़े पार्ट्स के लिए प्रोग्रेसिव प्रक्रिया अनुकूल न होगी क्योंकि बहुत बड़ी प्रेस और डाई की जरूरत पड़ेगी जो की काफी महंगे होंगे .
फोर स्लाईड प्रेसींग प्रक्रिया
फोर स्लाईड प्रेसींग प्रक्रिया से चौड़ाई में संकीर्ण पार्ट्स जैसे की क्लिप (clips), क्लैम्प (clamps), स्प्रिंग (springs) आदि बनते हैं. वायर (wire) से बने जटिल मोड वाले (complex bend) पार्ट्स इस प्रक्रिया से बनाए जाते हैं .
इस प्रक्रिया में संकीर्ण कॉईल फोर स्लाईड मशीन से गुज़रती हैं . मशीन में चार (कभी कभी चार से ज्यादा भी ) होतें हैं जो सीधी रेखा में निरंतर आगे -पीछे गतिमान होते हैं . ये स्लाईड प्रेस मशीन के रैम (ram) की भाँती कार्य करते हैं और कॉईल को मोड़ते (bend) हैं . सारे मोड सम्पन्न होते ही एक रैम पार्ट को कॉईल से जुदा कर देता हैं .
रैम का आगे-पीछे होने का क्रम एवं समय (timing) आवश्यकतानुसार विभिन्न कैम (cams) सेट कर के नियंत्रित किया जाता हैं .
इस प्रक्रिया से कम लागत पर तेजी से (high speed production) पार्ट्स का उत्पादन किया जाता हैं .
कई अन्य विशेषज्ञ प्रेसींग प्रक्रिया के दौरान पार्ट्स की 3-डी ज्यामिति (3D Geometry) के परिवर्तन के आधार पर प्रेसींग प्रक्रिया का वर्गीकरण निम्न चार्ट में दिखाया हैं उस प्रकार से करतें हैं :
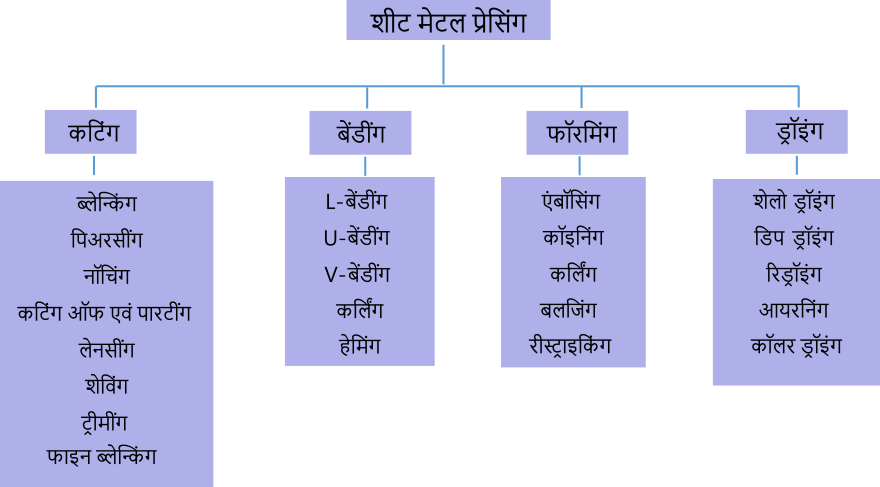
कटिंग प्रक्रिया (Cutting Operations)
शीट मेटल प्रेसींग में कटिंग में होता यह हैं की धातु की आंतरिक संरचना अपनी जगह से खिसक जाती हैं . कैंची से कागज़ काटना इसका सबसे जानामाना उदाहरण हैं . दूसरा परिचित उदाहरण हैं punching मशीन से कागज़ में छेद करना . इस प्रकार की काटने की प्रक्रिया shearing के नाम से जानी जाती हैं .
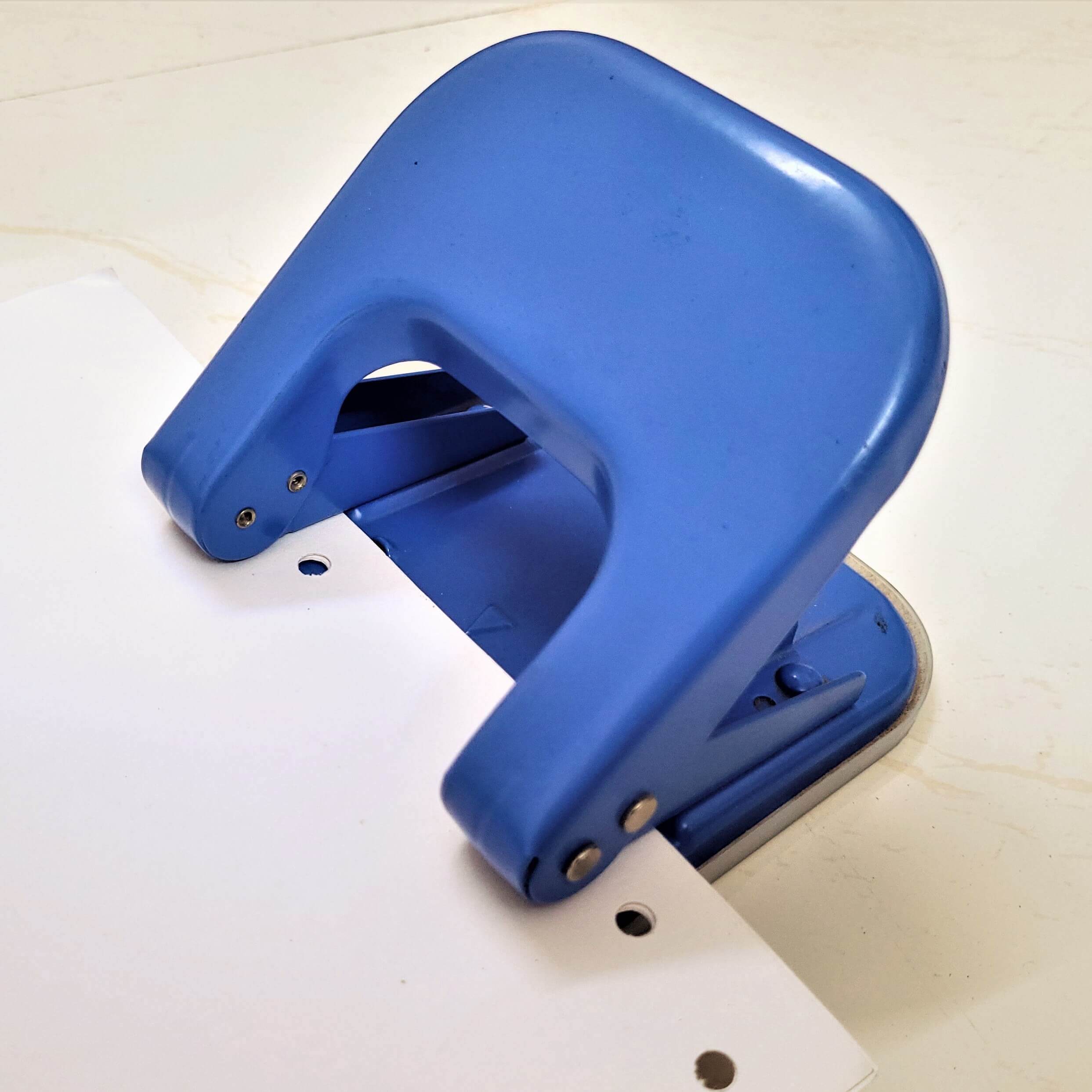
Paper punching machine Photo credit: Reena Shah
जब कैंची या punching मशीन का बल कागज़ की shear strength से अधिक हो जाता हैं तो आंतरिक संरचना फिसल कर खिसक जाती हैं और उस स्थान पर कागज़ कट जाता हैं.
जिस प्रकार कैंची में धातु की दो ब्लेडों की धारों के बीच फंसा कागज़ का हिस्सा कट जाता हैं उसी प्रकार से पंच और डाई की धारों के बीच फंसा धातु की शीट का हिस्सा पंच के तीव्र दबाव के कारण कट जाता हैं . cutting लाईन पर स्थित धातु की आंतरिक संरचना के दो हिस्से फिसलते हैं और खिसक कर एक दूसरे से अलग हो जाते हैं.
Shearing द्वारा कटिंग प्रक्रिया में क्या होता हैं यह निम्न आकृति में दर्शाया हैं :

शीट मेटल कटिंग प्रक्रिया के विभिन्न प्रकारों में सारी कटिंग बुनिया रूप से shearing failure से ही होती हैं . अब हम जानेंगे कटिंग के विभिन्न प्रकार क्या हैं .
Blanking ऑपरेशन (Blanking Operation)
कोई भी प्रेस पार्ट हो , पहला प्रेस ऑपरेशन blanking ही होता हैं . इसमे अपवाद यदि कोई हैं तो वो हैं प्रोग्रेसिव डाई में की हुई प्रेसींग जहाँ blanking सबसे आखिरी ऑपरेशन होता हैं. Blanking ऑपरेशन का उद्देश्य होता हैं शीट , कॉईल, पट्टी से सपाट (flat) blank बनाना. Blank वर्तुल , चोरस , आयताकार जैसे सरल एवं नियमित ज्यामितिक आकार के हो सकते हैं और जटिल अनियमित आकार के भी हो सकते हैं .
नीचे दिखाए चाबी के blank का आकार कई ज्यामितिक आकारों का संयोजन हैं. पहले चाबी की बाहरी outline के अनुसार blanking किया जाता हैं और उसके पश्चात अन्य ऑपरेशन जैसे की piercing , embossing वगैरह किए जाते हैं.
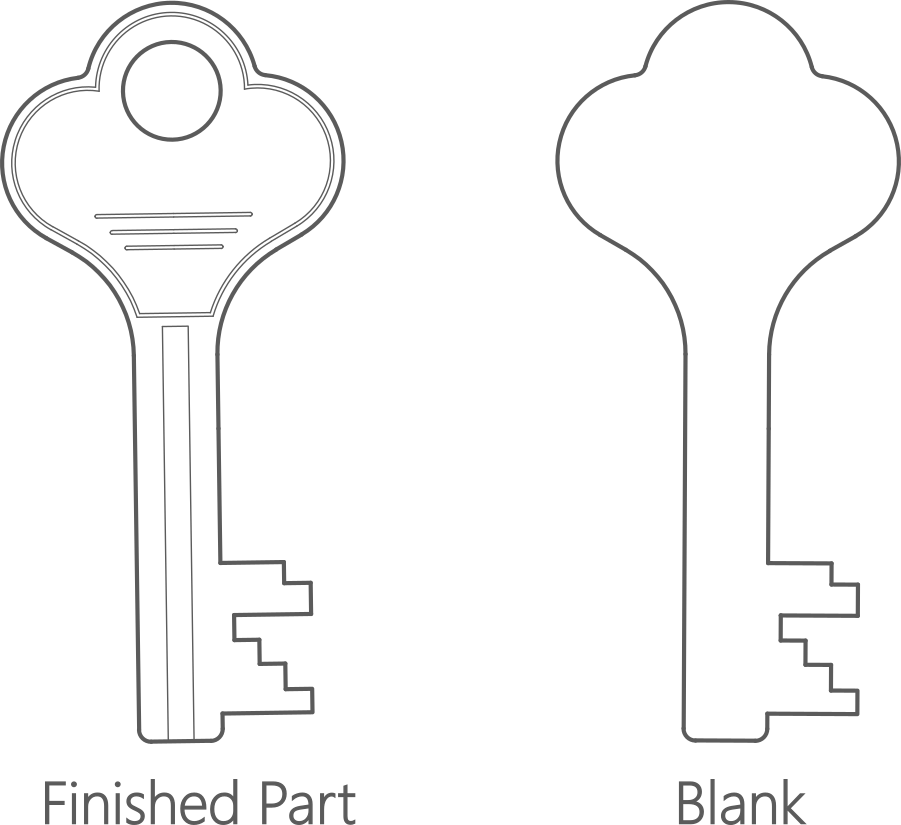
पट्टी (strip) से blank निकाल लेने के बाद जो मटीरीअल बच जाता हैं उसे स्क्रैप स्ट्रिप कहते हैं. स्ट्रिप में कितने पार्ट किस तरह बिठाए जाएं ताकि कम से कम स्क्रैप बचे इसके लिए जो योजना बनाई जाती हैं उसे स्ट्रिप लेआउट (strip layout) कहा जाता हैं. कईं स्ट्रिप लेआउट बनाए जाते हैं यह देखने के लिए की कौनसे layout से अधिकतम पार्ट प्राप्त किए जा सकते हैं. पार्ट की मटीरीअल cost न्यूनतम रखने हेतू अधिकतम पार्ट अर्जित करने वाला स्ट्रिप लेआउट चुना जाता हैं और इसके बाद ही blanking डाई डिज़ाईन की शुरुआत की जाती हैं.
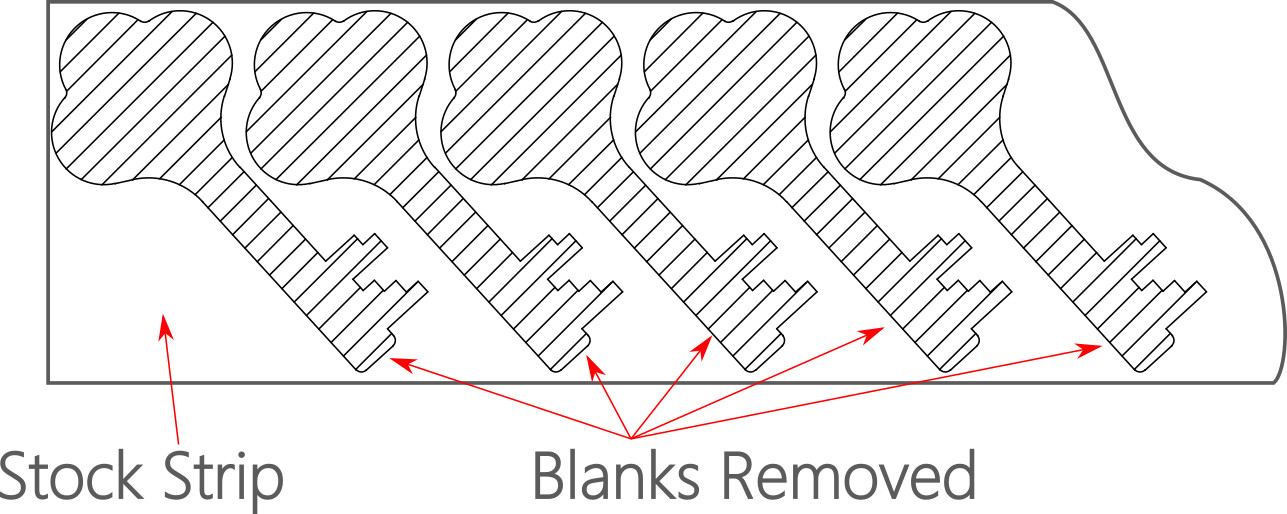
Piercing ऑपरेशन (Piercing Operation)
Piercing ऑपरेशन वो हैं जिसमें पार्ट में से कुछ हिस्से काट कर निकाल लिए जाते हैं.
कईं प्रेस पार्ट्स में विभिन्न आकार एवं साईज़ के छेद/सुराख (holes,cutouts,openings) पाएं जाते हैं. इनकी कुछ न कुछ उपयोगिता होती हैं. कभी-कभी केवल पार्ट को सुंदरता बनाने हेतू भी इनका प्रयोग किया जाता हैं. चाबी में जो छेद हैं उसकी उपयोगिता हैं.
नीचे दी गई चाबी की आकृति में blanking के बाद piercing किया हुआ दिखाया हैं. Piercing का आकार गोल हैं. यहाँ चाबी उपयुक्त पार्ट हैं और छेद से निकला गोलाकार material स्क्रैप हैं.
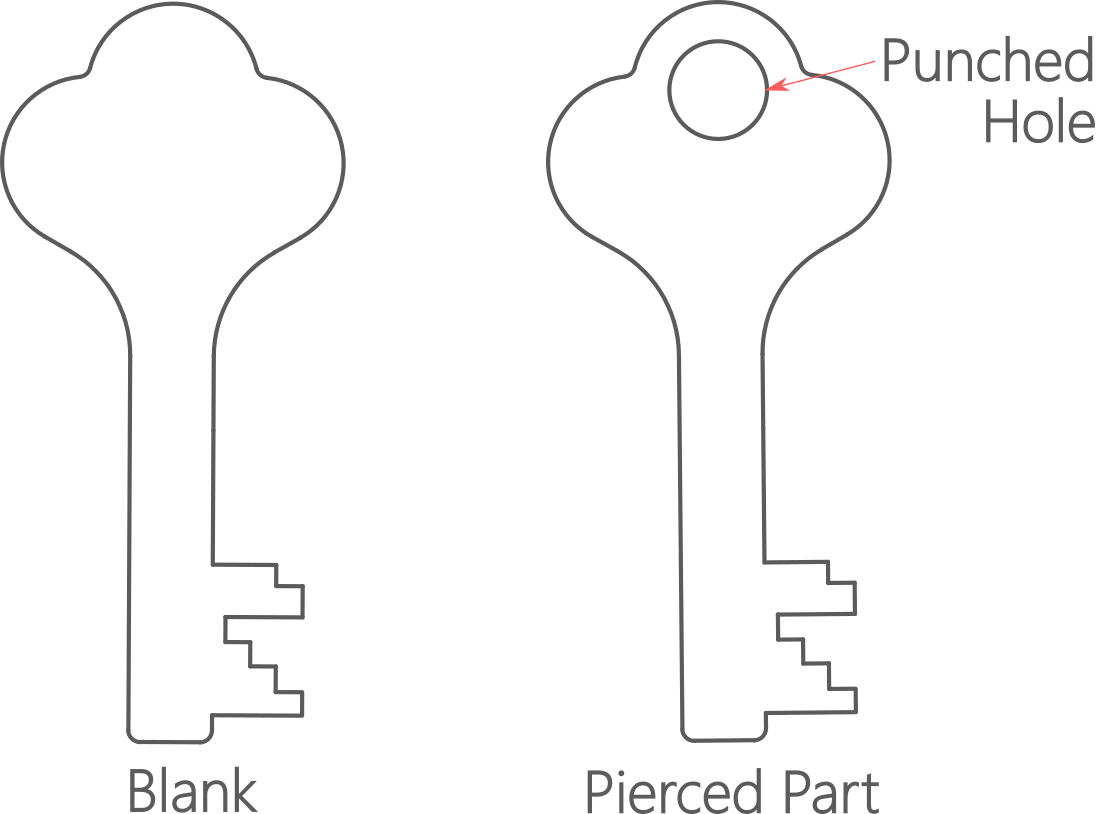
यह आवश्यक नहीं की piercing गोलाकार ही हो. बेहद जटिल, नाजुक एवं अनियमित ज्यामितिक आकार के छेद भी piercing ऑपरेशन से बनाए जाते हैं, जैसे की नीचे चित्र में दिखाया गया हैं.

Blanking और piercing ऑपरेशन में क्या अंतर हैं? दोनों ही कटिंग ऑपरेशन हैं परन्तु piercing में जो कट कर जुदा हो जाता हैं वो स्क्रैप होता हैं और blanking में जो कट कर जुदा हो जाता हैं वो उपयुक्त पार्ट होता हैं.
Piercing को कुछ लोग punching भी कहते हैं जो सही हैं.
Notching ऑपरेशन
Notching उस प्रेस ऑपरेशन का नाम हैं जिसमें सपाट समतल blank के बाहरी किनारों से कटिंग कर के material निकाल लिया जाता हैं. इस भेद को छोड़ दे तो notching बिल्कुल वैसा ही हैं जैसे की blanking और piercing. ऐसा नहीं हैं की सपाट blank पर ही notching हो सकती हैं. Notching अक्सर घुमावदार सतहों (curved surfaces) पर भी की जाती हैं.
Bending और Flanging ( किनारे पर किया हुआ 90 डिग्री वाला bending) ऑपरेशन से पहले notching ऑपरेशन का व्यापक रूप से उपयोग किया जाता हैं क्योंकि ये bending मे सरलता प्रदान करता हैं. इलेक्ट्रिक एवं इलेक्ट्रानिक्स प्रोडक्ट के बाहरी कैबिनेट एवं बक्सों में notching पाईं जाती हैं. निम्न आकृति में दिखाया गया हैं किस तरह V-notch से bending में आसानी रहती हैं .
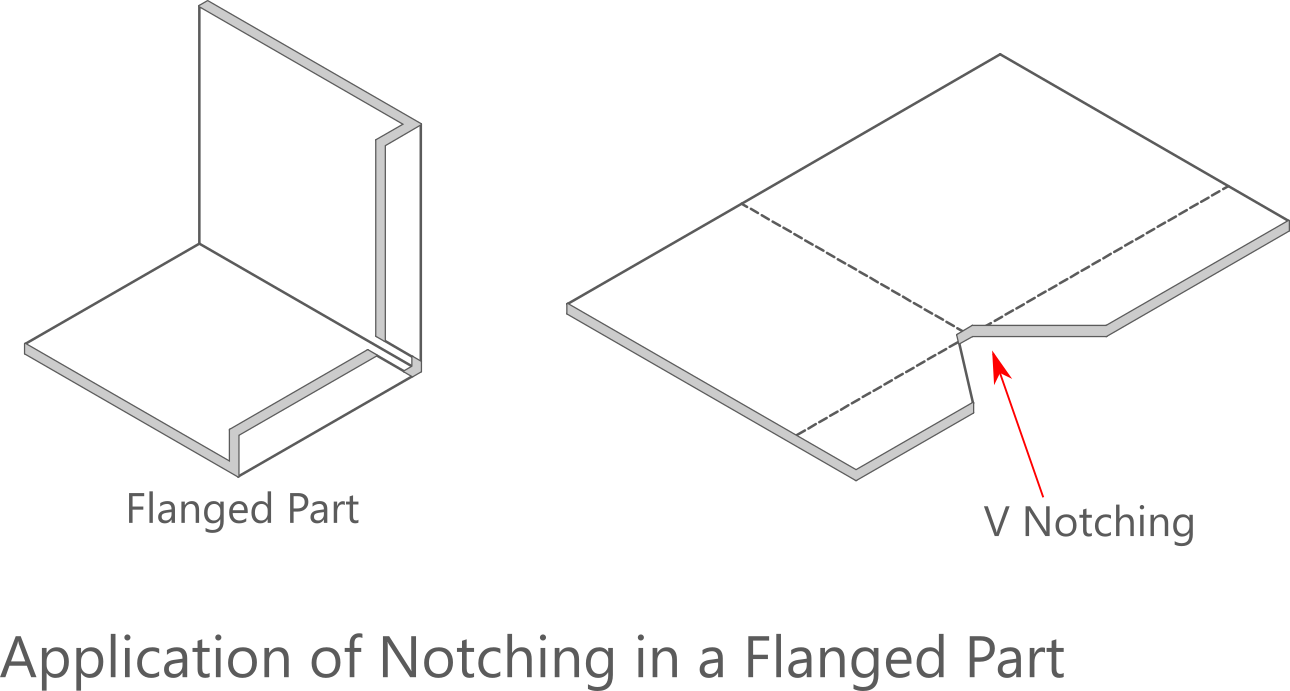
कॉर्नर notching किस प्रकार से बक्से की bending में उपयुक्त होती हैं यह निम्न आकृति से स्पष्ट होता हैं.

Notching का प्रयोग केवल bending तक ही सीमित नहीं हैं – इसका प्रोग्रेसिव डाई में भी उपयोग होता हैं अपितु बहुत भिन्न तरीके से. प्रोग्रेसिव डाई में notching स्टेशन सबसे पहले रखा जाता हैं. इससे एक स्थिर progression अंतर बनाए रखने में बहुत सुगमता रहती हैं.
Progression याने क्या ? प्रोग्रेसिव डाई में इसका क्या महत्व है ?
नीचे की आकृति 1 में 3 स्टेशन वाली वाशर की डाई की पट्टी दिखाई हैं. आरंभ में यह पट्टी डाई के ऊपर रखी हुई हैं. एक स्टापर (stopper) डाई पर लगा हुआ हैं. पट्टी का कोना स्टापर से सटा हुआ हैं. यह गोल वाशर की प्रोग्रेसिव डाई हैं इसलिए छेद (hole , सुराख) बनाने हेतू एक पिअरसिंग (piercing) स्टेशन का और बाहरी गोल कटाई हेतू एक ब्लेन्किंग (blanking) स्टेशन का प्रावधान किया गया हैं. इनके अलावा एक अतिरिक्त स्टेशन का भी प्रावधान किया गया हैं जो नॉचिंग (notching) करने हेतू इस्तेमाल होगा. नोच की लंबाई ‘P’ से दिखाई हैं. अभी प्रेस का रैम (ram) ऊपर ही रुका हुआ हैं. इस स्थिति में piercing station एवं notching station पट्टी से ढंके हुए हैं जबकी blanking स्टेशन बिल्कुल खुला पड़ा हैं.
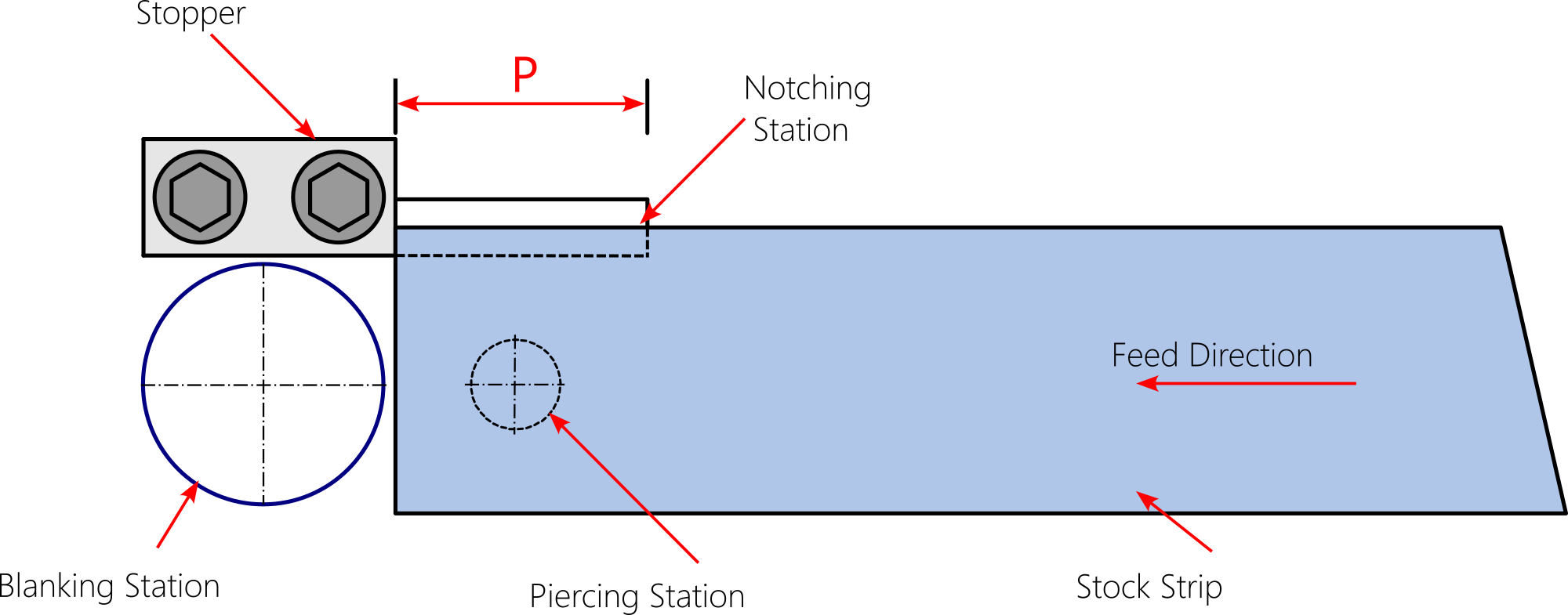
आकृति 1
जैसे ही प्रेस का ram नीचे आता हैं , पहला piercing और पहला notching ऑपरेशन अपने अपने स्टेशन पर हो जाते हैं. आकृति 2 देखें . स्टापर से सटा पट्टी का हिस्सा notching होते ही गायब हो जाता हैं. साथ ही पट्टी के notch में एक कोना ‘A’ भी बन जाता हैं. अब पट्टी feed की दिशा (feed direction) में जब आगे की ओर बढ़ाने में कोई रुकावट नहीं हैं. प्रेस का रैम ऊपर जाकर ठहर जाता हैं. . .
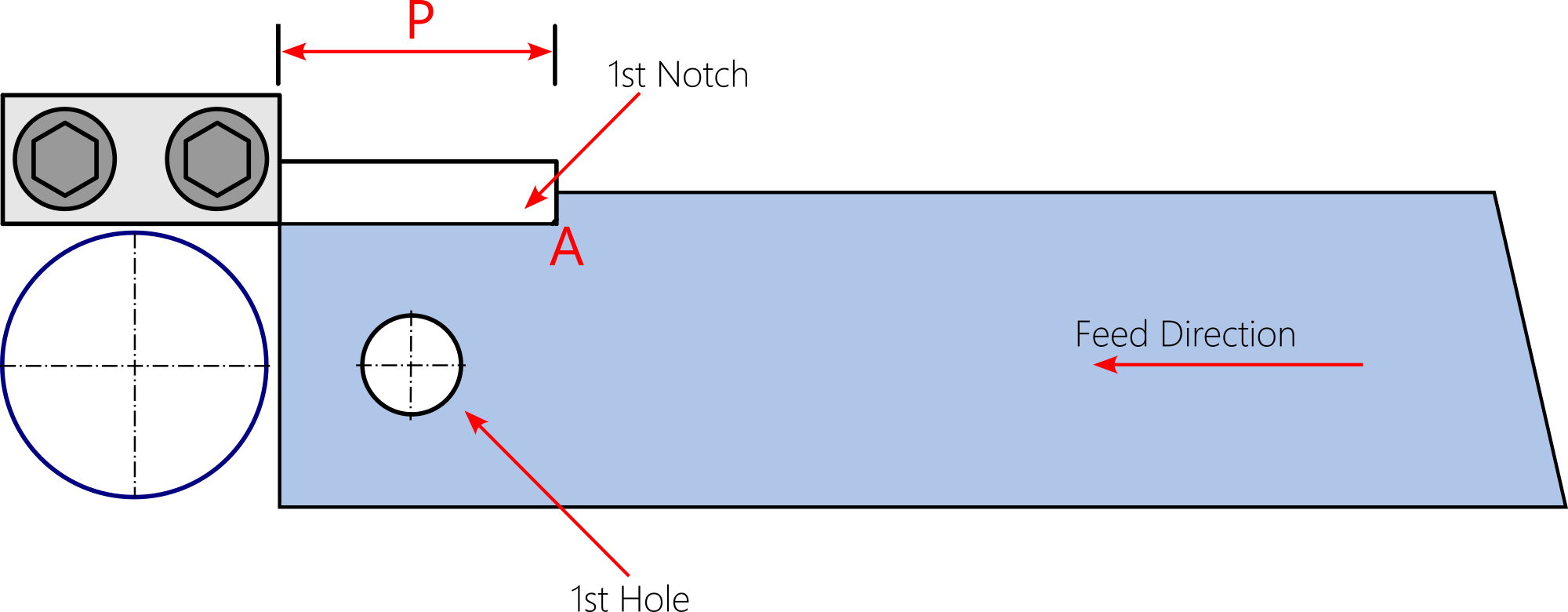
आकृति 2
आकृति 3 में दिखाया हैं की पट्टी feed direction में आगे बढ़ चुकी हैं , कोना ‘A’ स्टापर से सटा हुआ हैं और पट्टी का piercing वाला हिस्सा यानि की सुराख ब्लेन्किंग स्टेशन के ऊपर बिल्कुल सेंटर में आ चुका हैं. ये तो स्वाभाविक हैं कि सुराख भी उसी अंतर से आगे बढ़ा होगा जितना की कोना ‘A’. इधर notching एवं piercing स्टेशन के ऊपर पट्टी का नया हिस्सा आ चुका हैं. प्रेस का रैम अगले स्ट्रोक के लिए तैयार हैं.
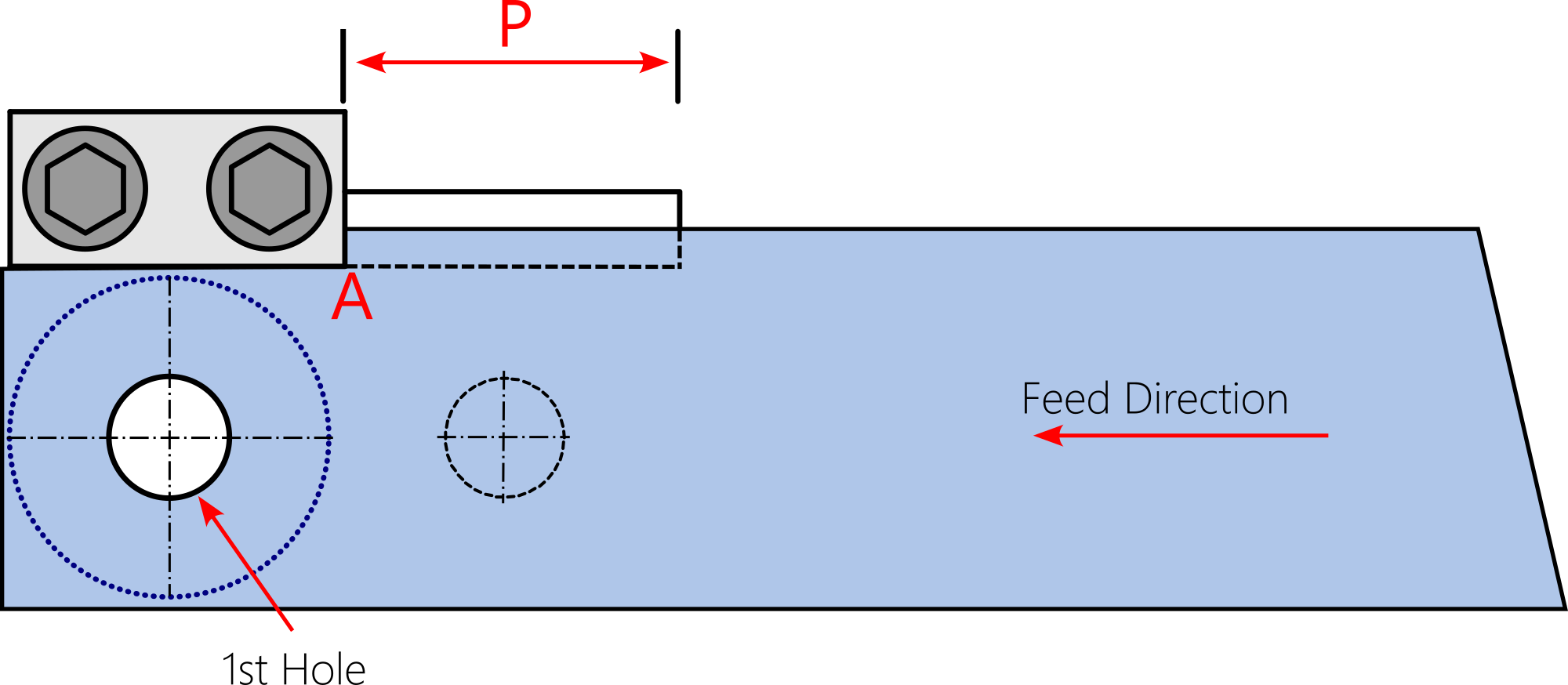
आकृति 3
नीचे की आकृति 4 देखें . अबकी बार रैम नीचे आकार स्ट्रोक लगाता हैं तो दूसरी नाच , दूसरा सुराख और पहला ब्लेन्किंग अपने अपने स्टेशन पर हो जाते हैं. ब्लेन्किंग स्टेशन से पहला वाशर बन कर नीचे गिर जाता हैं जो दाईं ओर दिखाया हैं. यही क्रम बारबार दोहराया जाता हैं. हर स्ट्रोक में एक नाच कटती हैं ; एक सुराख बनता हैं और एक पूर्णतया बना हुआ वाशर नीचे गिर जाता हैं. हर बार पट्टी सटीकता के साथ progression अंतर ‘A’ जितनी आगे बढ़ती रहती हैं.
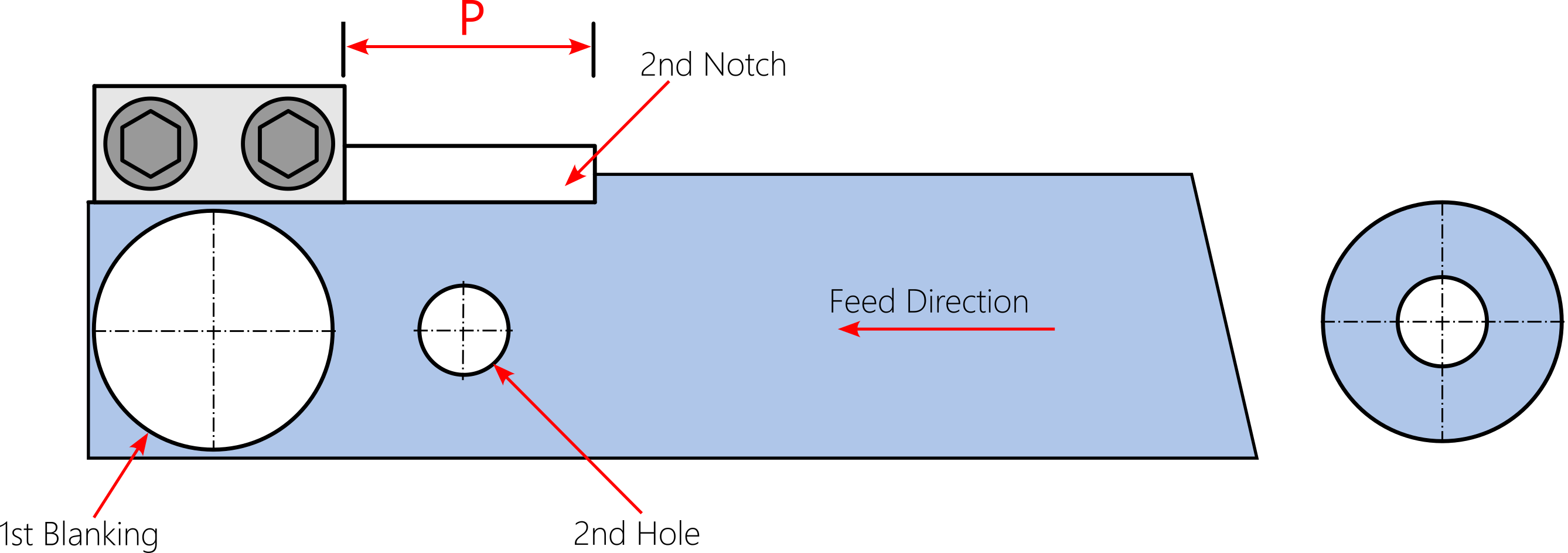
आकृति 4
इस प्रकार की स्टापर और पट्टी की जुगलबंदी को फ्रेंच (french) स्टापर कहा जाता हैं. फ्रेंच स्टापर को इस्तेमाल करने हेतू पट्टी की चौड़ाई पारंपरिक पट्टी की चौड़ाई से अधिक रखनी पड़ती हैं क्योंकि नॉचिंग हेतू कुछ अतिरिक्त मटीरीअल की आवश्यकता रहती हैं. पट्टी अधिक चौड़ी (100 mm से अधिक) हों तो आमने सामने स्थित दो फ्रेंच स्टापर की आवश्यकता रहती हैं. .
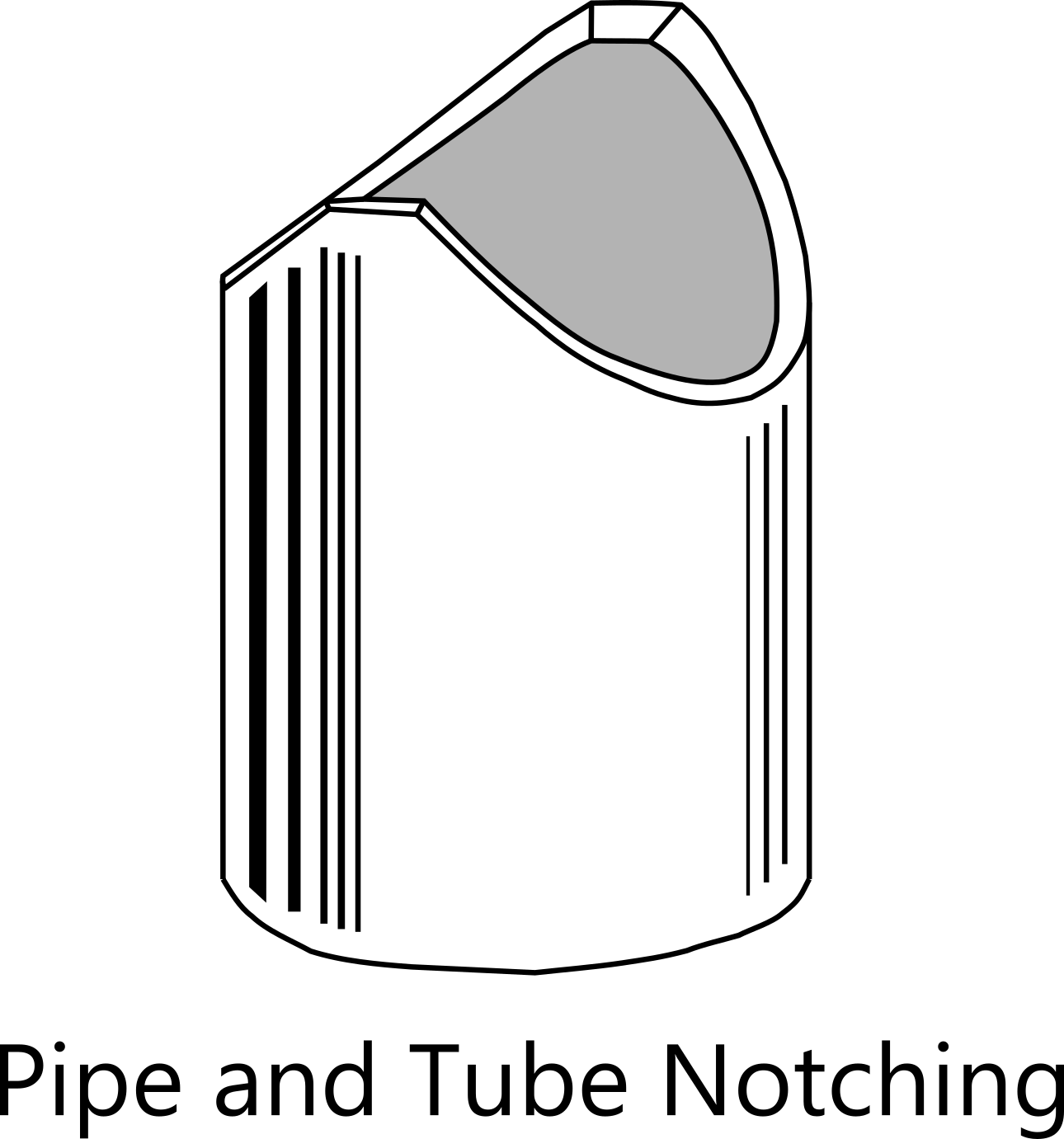
पाईप एवं ट्यूब के छोरों पर अक्सर notching पाईं जाती हैं. जब दो पाईप एक दूसरे के साथ वेल्डिंग के जरिए जोड़ने होते हैं तब किसी एक पाईप के छोर पर notching की जाती हैं .
Notching की वजह से वेल्डिंग से पहले पाइपों का आपस में अच्छी तरह से मिलान करना आसान हो जाता हैं और ऐसा जोड़ (joint) मजबूत भी होता हैं.
बगल वाली आकृति में एक और उदाहरण दिखाया गया हैं जिसमें घुमावदार सतह (curved surface ) पर notching की गई हैं.
यह automobile में लगने वाला बल्ब होल्डर हैं. यहाँ Notch का कार्य बल्ब बाहर की ओर निकल न आए यह सुनिश्चित करना हैं.
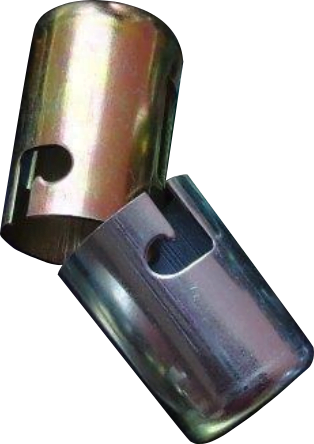
Cut-off और parting ऑपरेशन
एक सीधी या घुमावदार रेखा में कोई पार्ट काट कर पट्टी से अलग किया जाए तो उस cutting ऑपरेशन को cut-off ऑपरेशन कहा जाता हैं. Parting ऑपरेशन में भी यही होता हैं परन्तु थोड़ा फर्क हैं. Parting ऑपरेशन में दो सीधी या घुमावदार रेखाओं पर पार्ट काट कर पट्टी से अलग किया जाता हैं. Cut-off में स्क्रैप नहीं निकलता, जब की parting में स्क्रैप निकलता ही हैं.
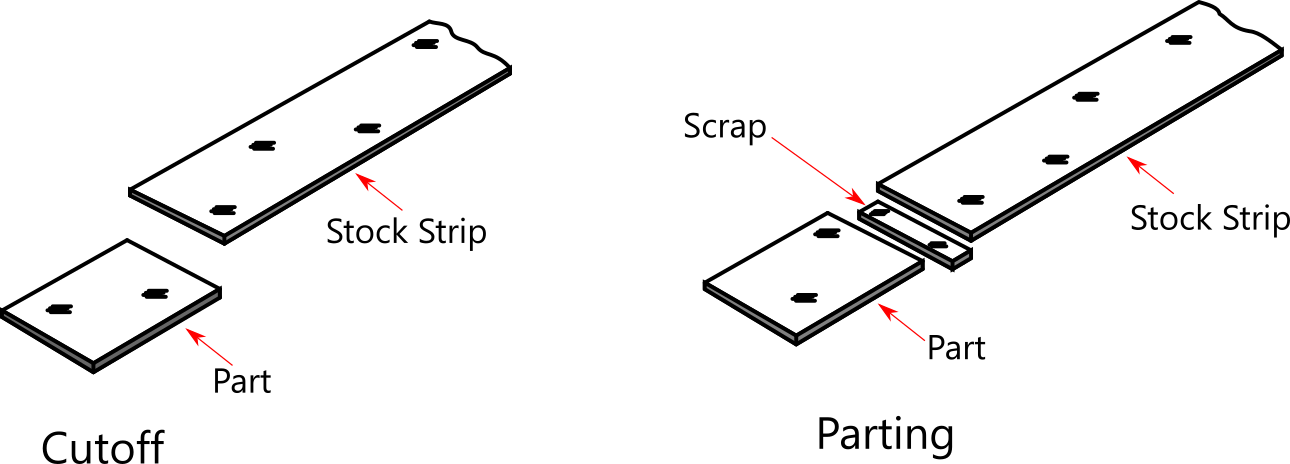
Cut-off ऑपरेशन बहुत किफायती होता हैं. क्योंकि इसमे कोई स्क्रैप नहीं निकलता. Cut-off पार्ट की दो sides पट्टी की sides के रूप में पहले से ही बनी होती हैं और तीसरी side पहले वाला पार्ट कटने पर पहले से ही बनी होती हैं. यदि यही पार्ट blanking ऑपरेशन से बनाया होता तो , नीचे वाली आकृति में दिखाया गया हैं वैसे पट्टी में ‘A’ से दर्शाया हैं उतना अतिरिक्त मटीरीअल रखना पड़ता. यानि की पट्टी की चौड़ाई ‘W’ न होती, ‘W+2A’ होती.
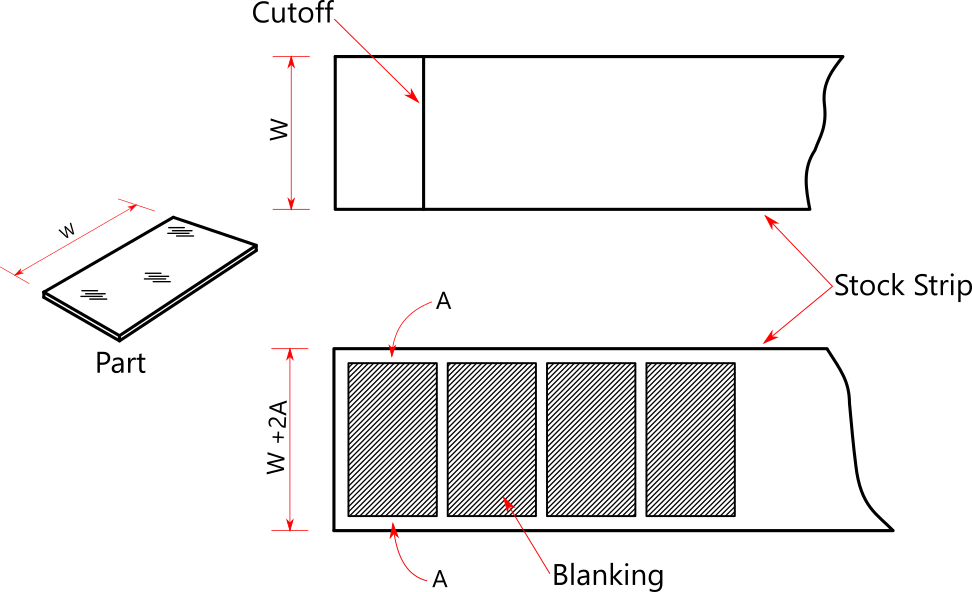
Cutoff ऑपरेशन की एक विशेषता हैं जो parting ऑपरेशन में नहीं हैं. निम्न आकृति से यह स्पष्ट हो जाएगा. Cutoff ऑपरेशन में होता यह हैं की पहले कटे पार्ट की पिछली side अगले पार्ट की आगे वाली side बन जाती हैं. इस विशेषता का यदि रचनात्मक तरीके से पार्ट डिज़ाईन में उपयोग किया जाए तो जटिल पार्ट काफी सस्ते में बनाएं जा सकते हैं.
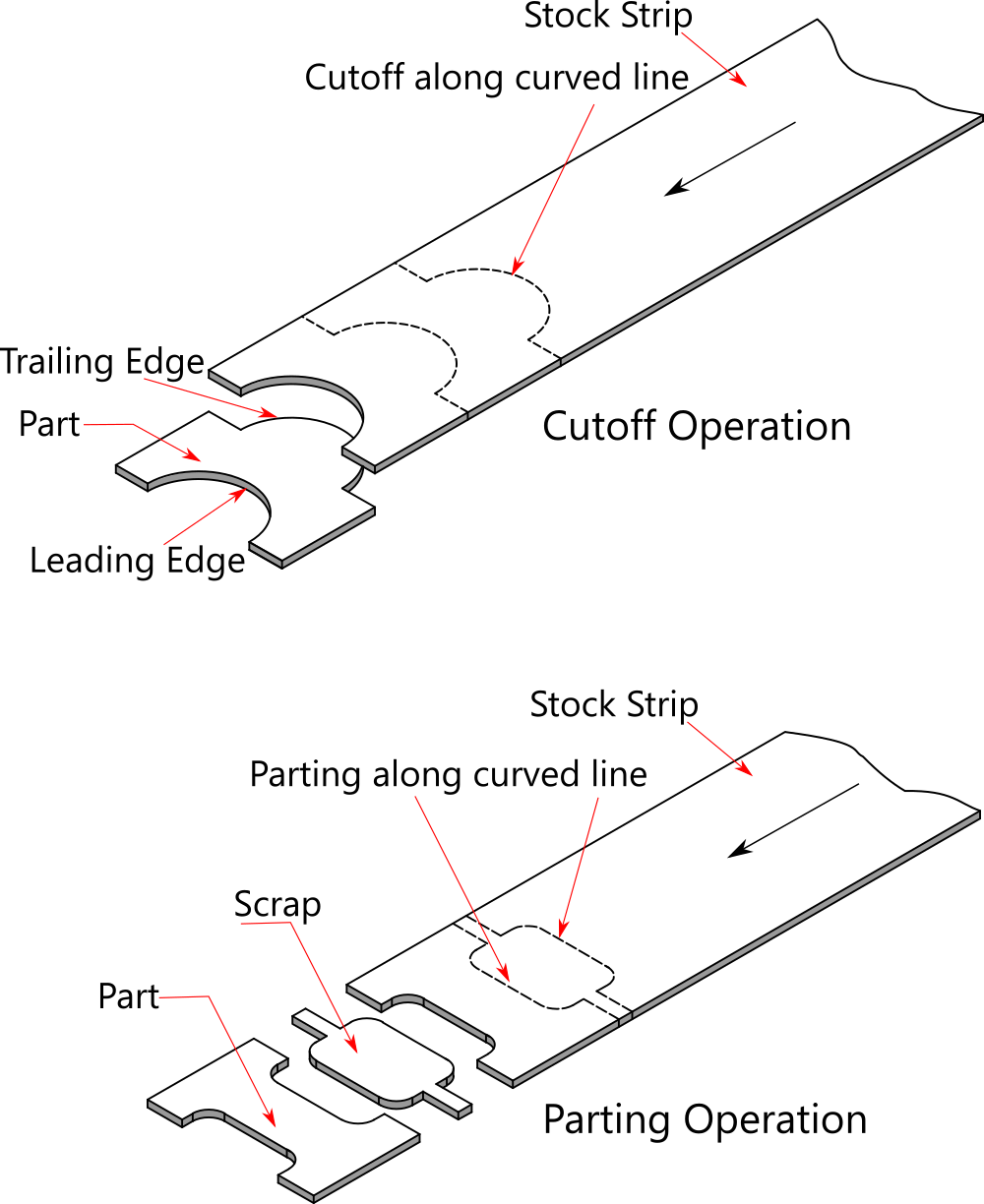
ऊपर वाली आकृति मे यह भी स्पष्ट देखा जा सकता हैं की cutoff ऑपरेशन में पंच की एक edge और parting ऑपरेशन में पंच की दो edge कटिंग करती हैं. Cutoff में पार्ट काटा जाता हैं जब की parting में स्क्रैप काटा जाता हैं !
Lancing ऑपरेशन
Lancing ऐसा प्रेस ऑपरेशन हैं जिसमें तीन रेखाओं पर कटिंग होती हैं जबकी चौथी रेखा पर bending होती हैं. Lancing में कटिंग एवं bending दोनों ऑपरेशन एक साथ होते हैं. क्योंकि चार रेखाओं /बाजुओं में कटिंग नहीं की जाती , कटिंग वाला हिस्सा पार्ट से जुड़ा ही रहता हैं, अलग नहीं होता , जैसे की piercing या blanking में होता हैं.
lancing ऑपरेशन का उपयोग मुख्य रूप से पार्ट में टैब (tab), वेन्ट (vent), लुवर (Louvre) और ब्रिज (bridge) जैसी रचनाएं बनाने हेतू होता हैं. ये रचनाएं कुछ विशेष उद्देश्यों की पूर्ति करती हैं.
नीचे दो प्रकार की टैब रचनाएं दिखाई गई हैं – एक में bend हैं जबकी दूसरी में 90 के कोण पर खड़ा टैब हैं. पहले वाला टैब स्प्रिंग जैसी चीजों के हुक टाँगने हेतू बनाया जाता हैं जबकी दूसरा वाला किसी चीज का स्थान निर्धारित करने हेतू (locate करने हेतू) बनाया जाता हैं. इस प्रकार का tab मच्छर भगाने वाली अगरबत्ती के साथ जो स्टैन्ड आता हैं उसमें आपने जरूर देखा होगा.
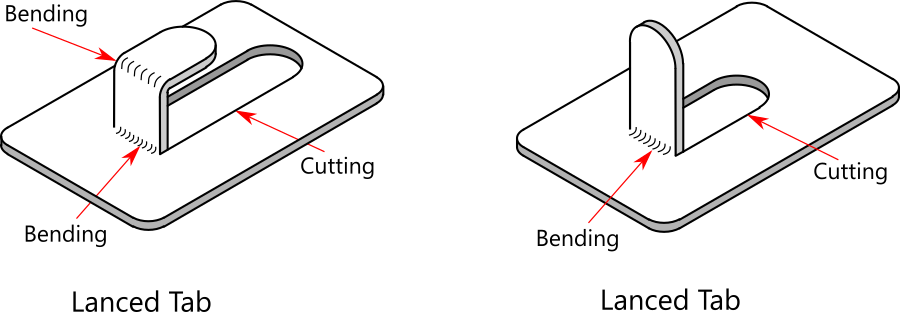
नीचे बाएं lancing की हुई वेन्ट दिखाई हैं. वेन्ट याने कोई ऐसी खिड़कीनुमा रचना जिसमें से हवा या तरल पदार्थ आ-जा सकते हों. Air Cooler के साइड पैनल पर हवा भीतर जाने हेतू जो लुवर (Louvre) बनाएं होते हैं वे भी एक प्रकार की वेन्ट ही हैं. दाएं ब्रिज रचना दिखाई हैं जो अन्य lancing रचनाओ से थोड़ी भिन्न हैं. ब्रिज में तीन नहीं केवल दो ही रेखाओं पर कटिंग होती हैं. यह कईं उद्देश्यों की पूर्ति करती हैं जैसे की यदि ब्रिज के मध्य में कोई चूड़ी वाला छेद हो तो स्क्रू लगाया हा सकता हैं. ब्रिज के मध्य में शीट की मोटाई कुछ कम ही रहती हैं यह भी भिन्नता हैं. ब्रिज ही height अधिक रखने से वहाँ मटीरीअल पतला हो कर टूटने की संभावना बढ़ जाती हैं.

प्रेस पार्ट की असेम्बली (assembly) में दो पार्ट जोड़ने से पहले उनके स्थान सटीकता के साथ निर्धारित करना आवश्यक होता हैं. नीचे दी गई आकृति में पार्ट B में टैब हैं और पार्ट A में piercing की हुई खिड़कियाँ हैं. असेम्बली के समय tab खिड़कियों में धँसने के साथ ही दोनों पार्ट के स्थान निर्धारित हो जातें हैं और इसके चलते असेम्बली सटीक बनती हैं. इस तरह से असेम्बली में lancing रचनाएं प्रयुक्त की जा सकती हैं.
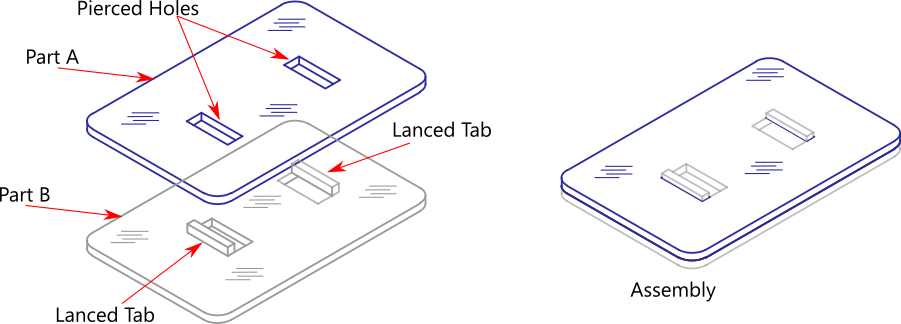
Shaving ऑपरेशन
Shaving ऐसा प्रेस ऑपरेशन हैं जिसमें पहले ही blanking या piercing किए हुए पार्ट के किनारों (edges) से बहुत ही छोटी मात्रा में मटीरीअल काटने हेतू पुन: कटिंग की जाती हैं.
छोटी-छोटी , पतली एवं महीन स्क्रैप जिसे स्लिवर (sliver) कहते हैं वे निकलती हैं. पार्ट के किनारे करारे, सपाट, एकदम साफ और सीधे करने हेतू shaving ऑपरेशन किया जाता हैं. किनारों की गुणवत्ता (quality) में बढ़ोतरी होती हैं और पार्ट के सटीक dimensions भी प्राप्त होते हैं. यह secondary ऑपरेशन यानि की दोय्यम (मुख्य नहीं) ऑपरेशन होता हैं. Primary (मुख्य) ऑपरेशन blanking या piercing या दोनों ही हो सकते हैं. नीचे दाईं आकृति में shaving ऑपरेशन दिखाया गया हैं.
कईं बार shaving और trimming ऑपरेशन की भिन्नता को लेकर भ्रमित हो जाते हैं. बर्तन , कप आदि जैसे ड्रॉ किए हुए पार्ट्स के किनारे अक्सर अनियमित एवं असमतल (irregular and uneven) होते हैं जिन्हे ठीक करने हेतू बाहर से छोटी सी रिंग की कटिंग होती हैं. इस रिंग के लिए पहले से ही अतिरिक्त material का प्रावधान किया होता हैं. अतिरिक्त material की कटिंग को trimming कहा जाता हैं. इस से विपरीत shaving में उसी material को पुन: काटा जाता हैं, अपितु बहुत ही कम मात्रा में.
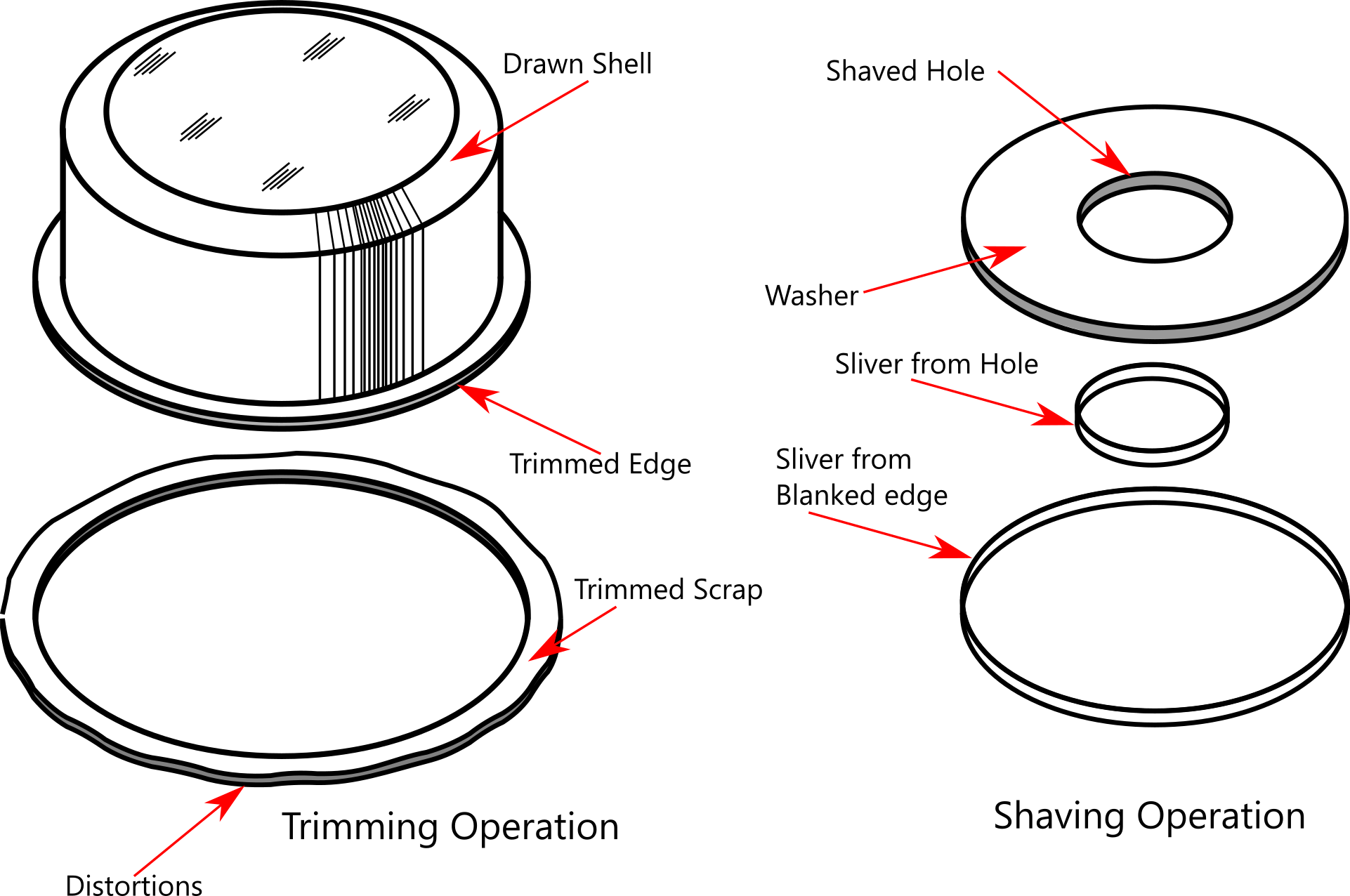
Shaving ऑपरेशन का एकमात्र उद्देश्य हैं किनारों की सटीकता. इस प्रकारकी सटीकता की आवश्यकता शीट मेटल से बने gears , घड़ी के पार्ट्स , business machine के पार्ट्स , instruments के पार्ट्स आदि में रहती हैं.
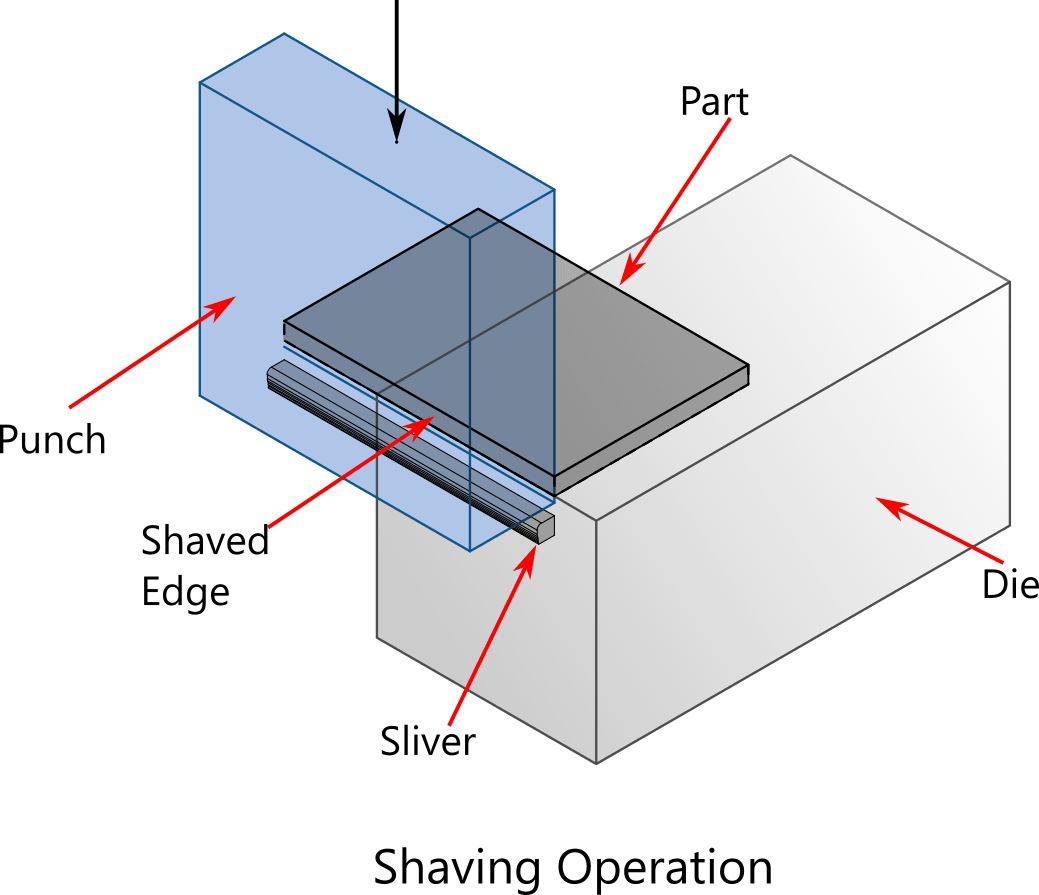
Blanking एवं piercing ऑपरेशन में किनारे सीधे, सपाट और समतल नहीं होते. कटिंग जहाँ से शुरू होती हैं वहाँ पार्ट के किनारे (edge) पर पहले radius बनती हैं , उसके बाद एक चमकीला बैंड (burnished band) होता हैं और आखिर में जहाँ से मटीरीअल टूट कर अलग होता हैं वहाँ खुरदरा , भीतर की ओर झुकता हुआ बैंड होता हैं, जैसे दाईं ओर नीचे की आकृति में दिखाया गया हैं. यह किनारे shaving ऑपरेशन के बाद कैसे सटीक बन जाते हैं यह बाईं ओर की आकृति में दर्शाया गया हैं.
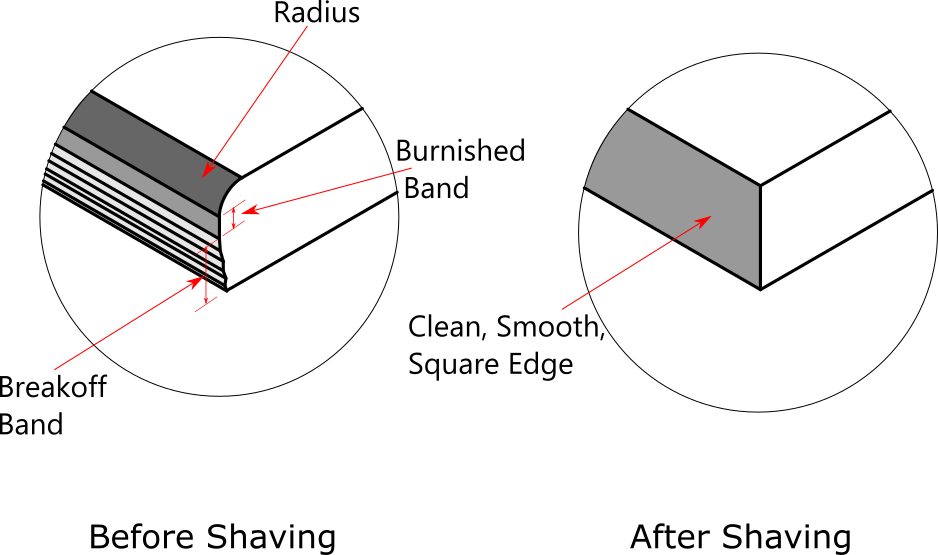
Shaving डाई बनाने में बहुत कौशल की आवश्यकता रहती हैं क्योंकि उसमें clearance बहुत ही कम रखा जाता हैं. अत्यधिक कम clearance की वजह से shaving डाई बनाना बहुत चुनौतीपूर्ण होता हैं. डाई-पंच के बीच छोटी सी misalignment भी डाई को नुकसान पहुँचा सकती हैं, डाई-पंच के किनारों का तीखापन (sharpness) नष्ट हो जाता हैं और उस जगह पार्ट में बाबरी (burr) आ जाती हैं.
Trimming ऑपरेशन
Trimming ऐसा प्रेस ऑपरेशन हैं जिसमें ड्रॉ और forming किए हुए पार्ट्स के परिधीय (peripheral) हिस्से से रिंग नुमा स्क्रैप material काट कर अलग किया जाता हैं. यह हिस्से अनियमित,लहरदार (wavy) और असमतल होते हैं. ऐसे पार्ट्स quality के दृष्टिकोण से स्वीकार्य नहीं हो सकते. Draw और forming ऑपरेशन में यह समस्या बहुत आम हैं. नीचे की आकृति में trimming ऑपरेशन का एक अतिसामान्य उदाहरण दिखाया गया हैं.
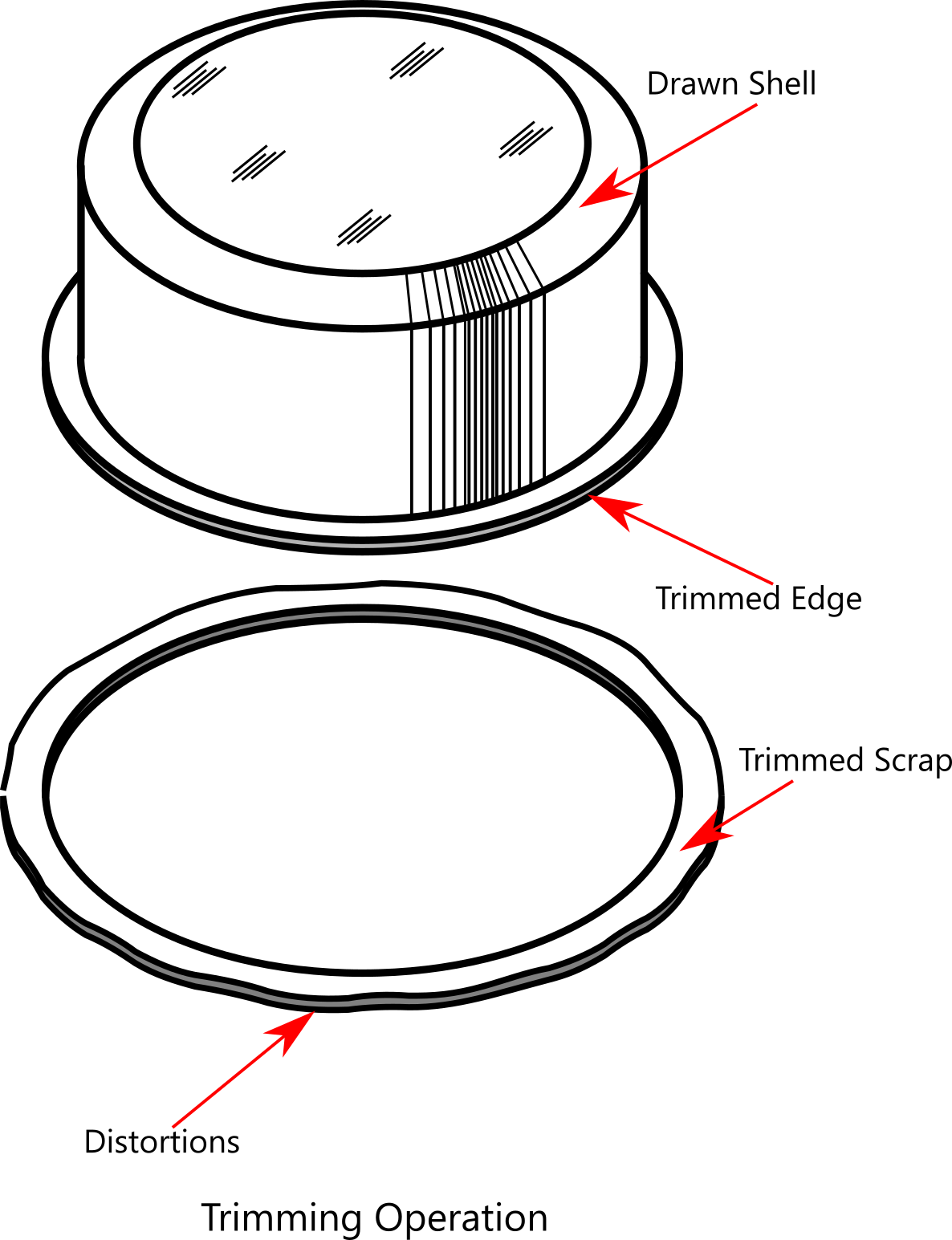
रसोई में इस्तेमाल होने वाले कईं बर्तनों में किनारे बाहर की ओर निकले होतें हैं ताकि बर्तन ठीक तरह से हाथों से पकड़ा जा सके. इन किनारों कों प्रेस टेक्नॉलजी की भाषा में फ्लैन्ज (flange) कहा जाता हैं. वे trimming ऑपरेशन द्वारा बनाएं जातें हैं. इनको बनाने के लिए गोलाकार trimming डाइयों का इस्तेमाल किया जाता हैं क्योंकि सामान्यतया बर्तन गोलाकार ही होतें हैं. अपितु automobile इंडस्ट्री में ड्रॉ किए हुए या forming किए हुए पार्ट्स फ्लैन्जहिन (flangeless) भी होते हैं. फ्लैन्ज वाले और flangeless पार्ट्स का अंतर निम्न आकृति में दिखाया हैं.
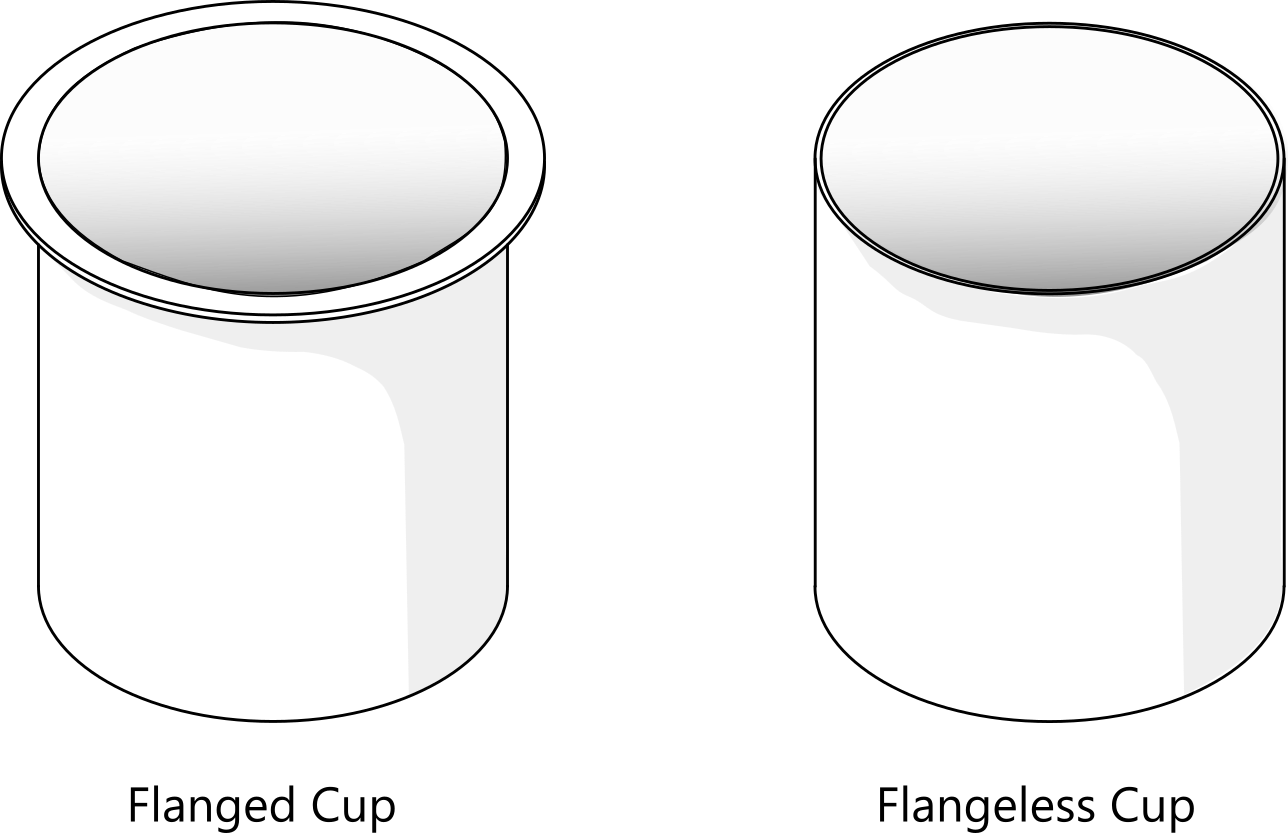
Trimming क्यों करें ? ड्रॉ किए हुए पार्ट्स के बाहरी किनारे trimming करने की आवश्यकता ही न हों ऐसा नहीं हो सकता ? गोल आकार की फ्लैट blank की सटीक साईज़ निकालना ज्यादा मुश्किल नहीं हैं. इसलिए उनकी सटीक blank साईज़ निकाली जाती हैं. परन्तु बात जब अनियमित आकारों की या आयताकार पार्ट की हों तो उनकी सटीक blank साईज़ निकालना बहुत चुनौतीपूर्ण काम होता हैं. इसमे बहुत सारे ट्रायल करने पड़ते हैं. प्रत्येक ट्रायल के बाद blank साईज़ में सोच कर बदलाव करने पड़ते हैं. बार बार संशोधित blank कटवाने पड़ते हैं. बहुत मेहनत और समय भी लगता हैं. बहुत धीरज की आवश्यकता रहती हैं. तब एक-दो blank साईज़ निकालकर ऐसी साईज़ निर्धारित की जाती हैं की जिसमें कुछ अतिरिक्त मटीरीअल trimming हेतू जानबूझ कर छोड़ रखा होता हैं. ड्रॉ के बाद trimming के जरिए यह अतिरिक्त मटीरीअल निकाल लिया जाता हैं. हालाँकि एक अतिरिक्त डाई ट्रिमिंग के लिए बनानी पड़ती हैं परन्तु सटीक blank साईज़ निकालने के लिए जो समय , मेहनत और खर्च लगता हैं वह बच जाता हैं.
नीचे आयताकार बॉक्स की trimming का उदाहरण दर्शाया हैं जिसमें सटीक blank साईज़ निकालने की मेहनत करने के बजाय trimming का सहारा लिया गया हैं.
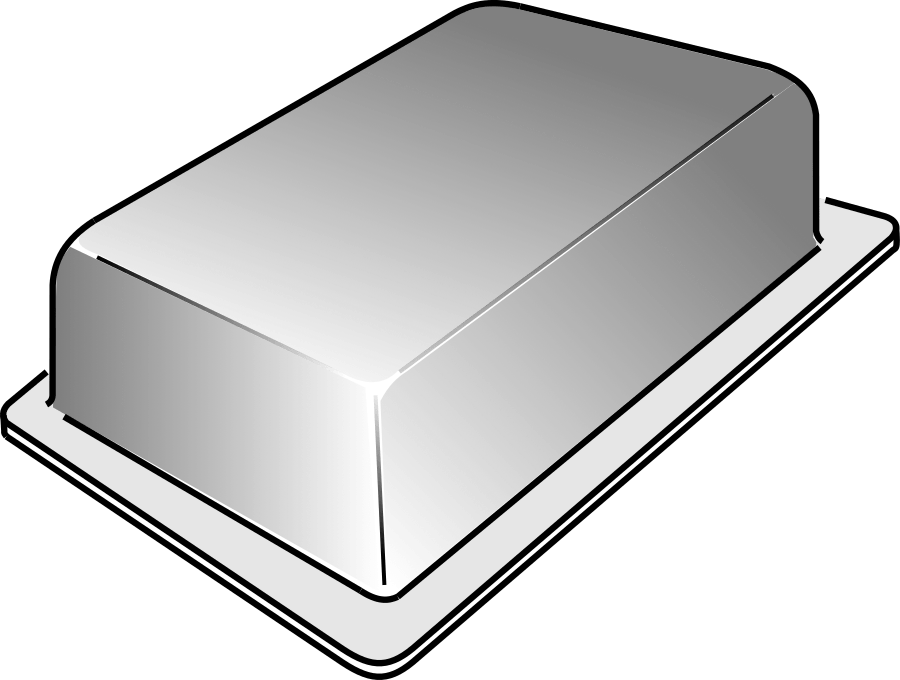
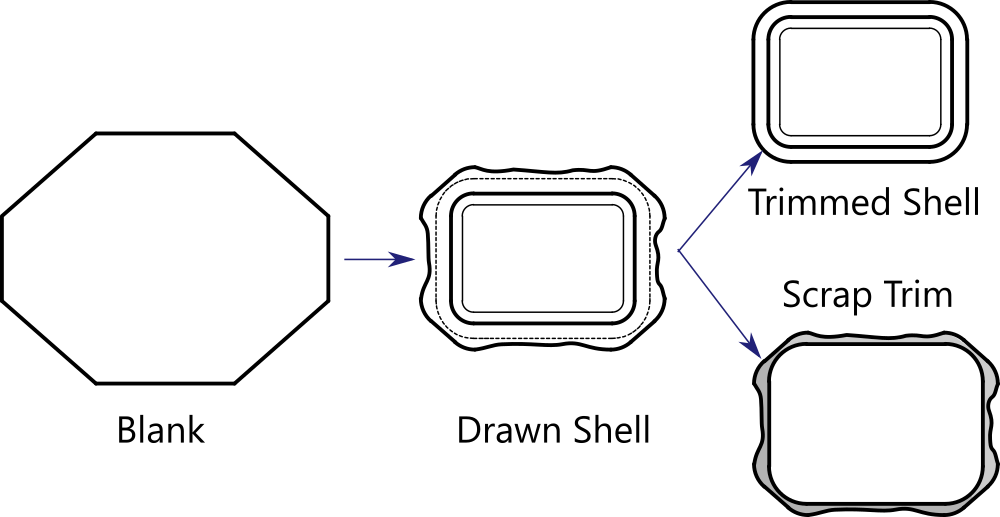
Trimming ऑपरेशन का एक विशेष प्रकार हैं जिसे पिन्च trimming कहते हैं. पिन्च का मतलब होता हैं चुटकी. जिस तरह चुटकी लेते समय तीव्र दबाव बनता हैं ठीक वैसे ही Pinch ट्रिमिंग में material को तीव्र दबाव से प्रेस किया जाता हैं जिसके फलस्वरूप material वहाँ टूट कर अलग हो जाता हैं. पिन्च ट्रिमिंग के लिए अलग से कोई डाई नहीं बनाई जाती – आखिरी ड्रॉ डाई के साथ ही उसे कम्बाइन किया जाता हैं. Flange-less पार्ट्स में सामान्य trimming नहीं किया जा सकता – पिन्च trimming का सहारा लेना पड़ता हैं या lathe मशीन पर किनारे बनाने होतें हैं. अपितु पिन्च ट्रिमिंग से प्राप्त हुई edge उतनी उन्नत किस्म की नहीं होती जितनी lathe मशीन पर बनाई edge होती हैं. कुछ चाकू-छुरी जैसी धारदार edge पिन्च ट्रिमिंग से मिलती हैं.
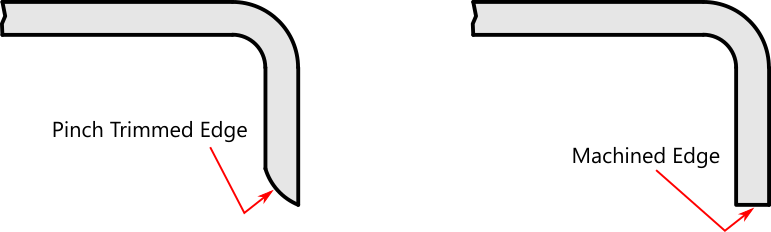
पिन्च ट्रिमिंग के लिए अलग से कोई डाई नहीं बनाई जाती – आखिरी ड्रॉ डाई के साथ ही उसे कम्बाइन किया जाता हैं.
Fine Blanking ऑपरेशन
Fine blanking एक ऐसा अनोखा प्रेस operation हैं जिसमें अति उत्कृष्ट edge quality , उच्च कोटी की पार्ट समतलता (flatness) और बेहतर dimensional टालरन्स (tolerance) प्राप्त की जाती हैं. शीट की मोटाई चाहे कितनी ही अधिक हों और production चाहे कितना ही ज्यादा हों , fine blanking ये सारी विशेषताएं प्रदान करता हैं.
पारंपरिक blanking से fine blanking कई मायनों में भिन्न हैं. इस प्रक्रिया में एक विशेष प्रकार की pressure रिंग का इस्तेमाल किया जाता हैं. इस pressure रिंग का , जिसे impingement रिंग भी कहते हैं , v -आकार वाला हिस्सा (grip) शीट के अंदर धँस कर उसे मजबूती से पकड़ कर रखता हैं ताकि blanking प्रक्रिया के दौरान शीट तनिक भी इधर-उधर हिलें नहीं. डाई के छेद में एक ejector होता हैं जो एक ram के जरिए कटे हुए पार्ट पर निरंतर ऊपर की ओर pressure बनाए रखता हैं. यह ejector ब्लैंक को ऊपर से बाहर निकालने में सहायता करता हैं. पारंपरिक blanking में जो clearance रखा जाता हैं उससे बहुत कम clearance यहाँ रखा होता है.
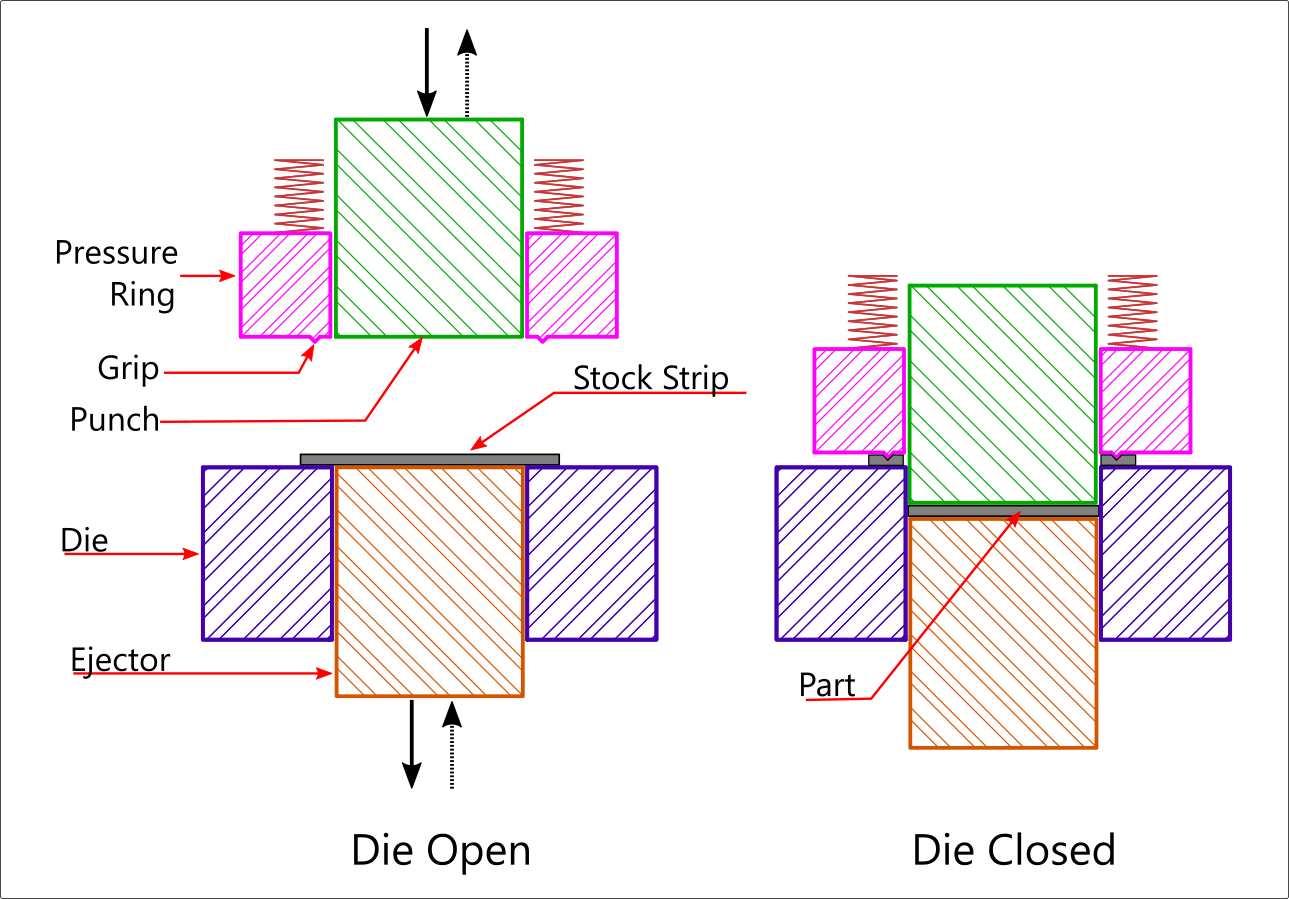
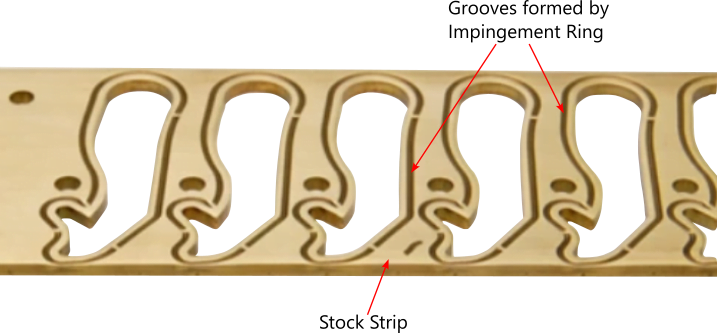
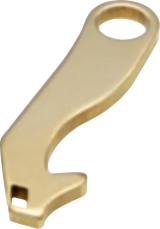
Fine blanked stock strip and part: Image credit: Swiss Tech Precision , Post Falls, Idaho Video
fineblanking किए हुए पार्ट के किनारों पर radius, बाबरी (burr) और taper ऊपर की सतह पर बनते हैं. यह पारंपरिक blanking वाले पार्ट से बिल्कुल ही विपरीत हैं. Fineblanking के लिए ट्रिपल एक्शन प्रेस (triple action press) यानि की 3 ram वाली प्रेस की आवश्यकता रहती हैं और प्रेस की tonnage भी अधिक होना आवश्यक हैं. इस वजह से fineblanking ऑपरेशन पारंपरिक blanking ऑपरेशन से अधिक खर्चीला होता हैं.
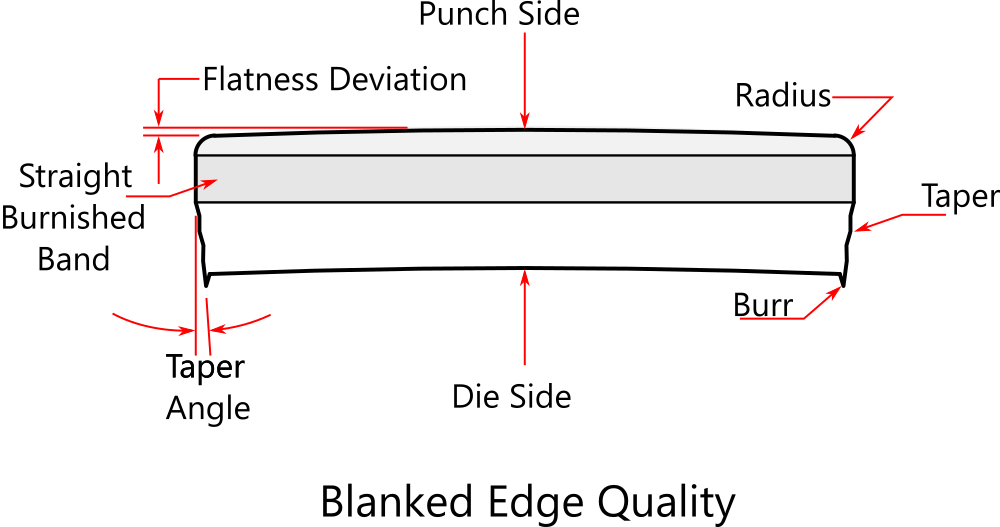
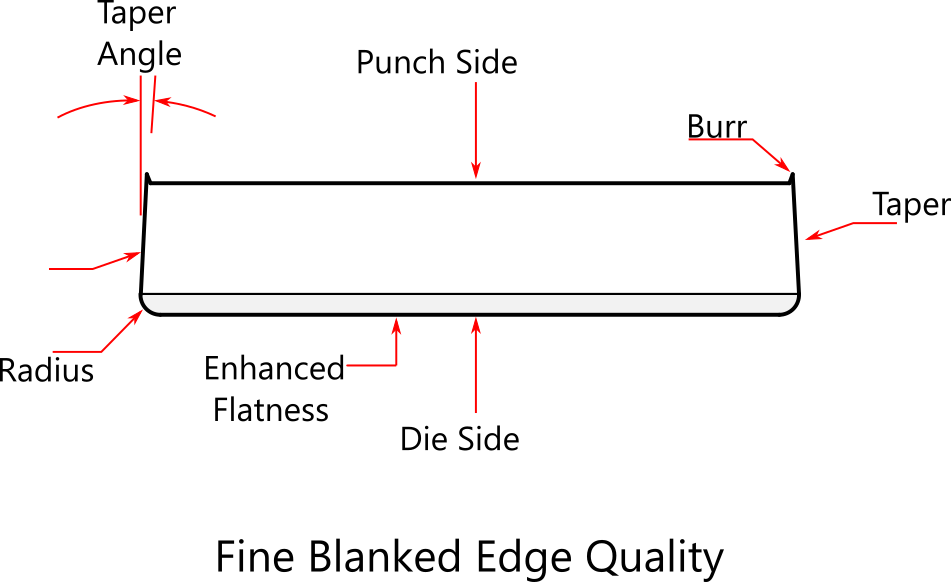
Fineblanking डाई पारंपरिक blanking डाई से 1.5 से 3 गुना महंगी होती हैं परन्तु fineblanking से जो बेहतर edge quality प्राप्त होती हैं उसकी वजह से पार्ट पर अन्य दोय्यम ऑपरेशन करने की आवश्यकता ही नहीं रहती. इसलिए fineblanking ऑपरेशन महंगा होने के बावजूद भी इसे पसंद किया जाता हैं.
ऑटोमोबाईल उद्योग में शीट मेटल gears, chain links , cams, क्लच प्लेट आदि कम्पोनन्ट जहाँ edge क्वालिटी का बहुत अधिक महत्व होता हैं वहाँ fineblanking के सिवा कोई विकल्प नहीं हैं.
Bending ऑपरेशन
Bending ऑपरेशन ऐसा प्रेस ऑपरेशन हैं जिस में material एक रेखा के इर्दगिर्द मोड कर आकार बनाया जाता हैं.
जहां सारे कटिंग ऑपरेशन में पार्ट के दो आयाम – लंबाई एवं चौड़ाई- बनते हैं वहीं bending ऑपरेशन में तीसरा आयाम -ऊंचाई (height) भी बन जाता हैं. शीट मेटल के विभिन्न ऑपरेशन में bending एक महत्वपूर्ण ऑपरेशन हैं.
blanking ऑपरेशन में फ्लैट blank का मूल plane दो या अधिक plane में विभाजित हो जाता हैं. Bending ऑपरेशन की विशेषता यह हैं की एक रेखा के इर्दगिर्द material जब मुड़ता हैं तो मोड पर भीतरी हिस्सा दबाव (compression) में और बाहरी हिस्सा खिंचाव (tension) में रहता हैं.
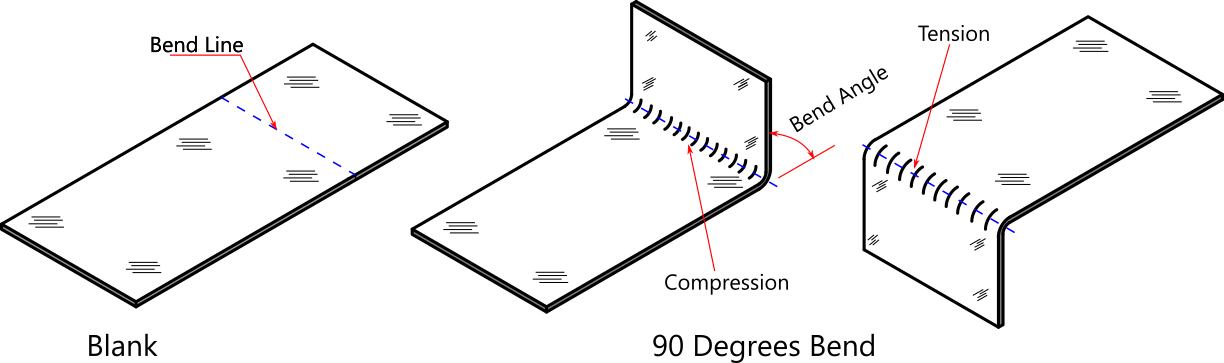
निम्न चित्र में विभिन्न प्रकार के bending वाले कम्पोनन्ट दिखाएं गए हैं. गौर करें की प्रत्येक bend एक सीधी रेखा (bending line) पर हैं , एक कम्पोनन्ट में एक से अधिक bend भी हो सकते हैं और wire (तार , राड ) भी bending द्वारा मोड़ा जाता हैं.
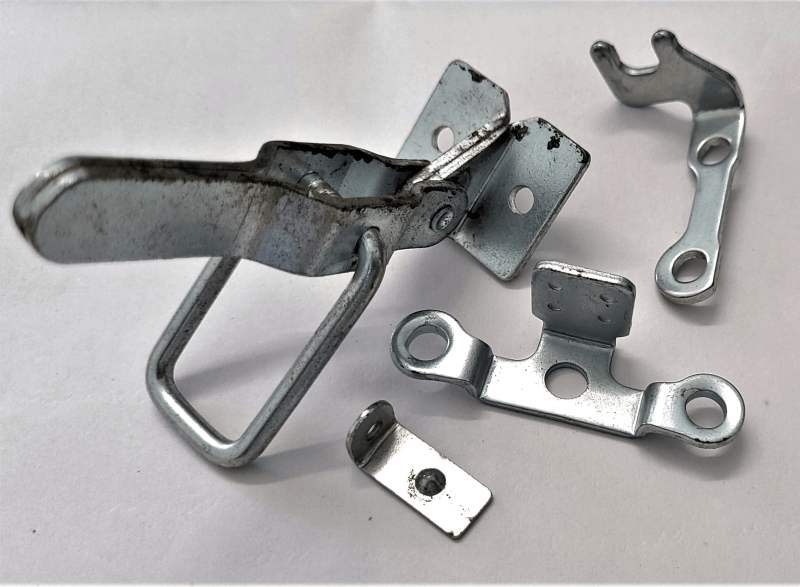
Bending से प्राप्त आकार के आधार पर bending ऑपरेशन के चार मुख्य प्रकार निम्न आकृति में दिखाएं गए हैं वे हैं L-bending , U-bending , V-bending और गोलाकार मोड (कर्लिंग Curling).
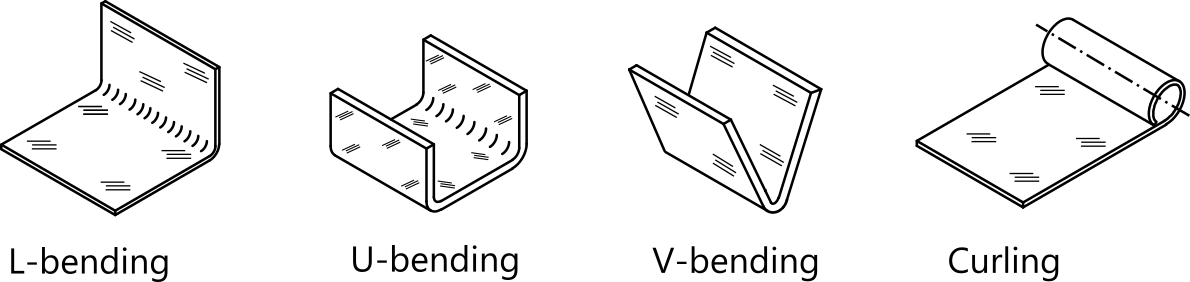
ज्यादातर शीट मेटल bend किए हुए पार्ट्स में इन विभिन्न bending के प्रकारों का संयोजन (combination) होता हैं. Bending का एक रोचक एवं बिल्कुल ही भिन्न प्रकार हैं जो पतले पार्ट्स के किनारों को मोटा करने हेतू प्रयुक्त होता हैं उसका नाम हैं हेमिंग (hemming).

हेमिंग ऑपरेशन में शीट की edge इतनी मोड दी जाती हैं की वह अंत में स्वयं के ऊपर ही फोल्ड (fold) हो जाती हैं. इस तरह वहाँ मोटाई (thickness) दुगनी हो जाती हैं.
पतली शीट इस तरह से 180 डिग्री bend करना मोटी शीट मोड़ने की अपेक्षा सरल होता हैं. पतले पार्ट्स के नुकीले किनारों से हाथों की त्वचा कटने की संभावना रहती हैं. ऐसे हालत में हेमिंग की हुई edge सुरक्षित मानी जाती हैं. हेमिंग की वजह से सुरक्षा तो मिलती ही हैं अपितु edge की ताकात (strength) भी बढ़ती हैं.
हेमिंग ऑपरेशन दो पतले पार्ट्स को जोड़ने (join) करने हेतू भी काम आता हैं. जैसे की ऊपर वाली आकृति में दाईं ओर दिखाया गया हैं की कैसे यह जोड़ (joint) बनता हैं. परन्तु hemmed joint केवल पतले कॉमपोनेन्टस में ही सम्भव हैं क्योंकि मोटी शीट 180 डिग्री मोड़ने पर bending में क्रैक (cracks) बन जाते हैं.
Forming ऑपरेशन
जिस प्रेस ऑपरेशन में सीधी रेखाओं की बजाय घुमावदार रेखाओं पर bending किया जाता हैं उस ऑपरेशन को forming ऑपरेशन कहा जाता हैं.
यह फर्क निम्न आकृति में दिखाया गया हैं.
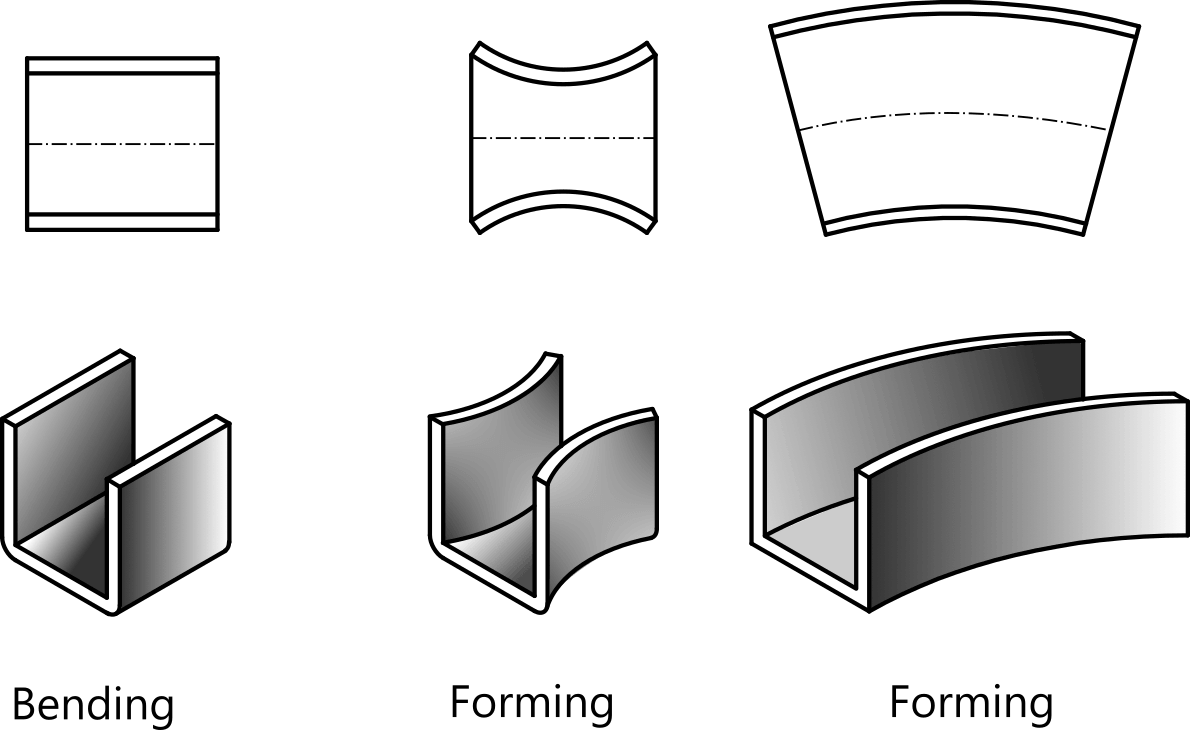
Forming ऑपरेशन की सबसे महत्वपूर्ण भिन्नता यह हैं की forming किए हुए पार्ट का आकार हूबहू पंच या डाई के आकार जैसा होता हैं. Bending में पार्ट और डाई या पंच के आकार एकसमान नहीं होते. Forming से बने कुछ आकारों (forms) में यह जरूरी होता हैं की पंच और डाई के उन हिस्सों का आपस में perfect मिलान हों जो पार्ट को प्रेस करते हैं – अपितु दोनों के बीच thickness जितनी गैप (gap) छोड़नी जरूरी हैं.
ड्रॉइंग के अनुसार पार्ट का आकार बनाने के अलावा forming ऑपरेशन कई अन्य उद्देश्यों की पूर्ति हेतू भी किया जाता हैं. उदाहरण के लिए, पार्ट का सौन्दर्य बढ़ाने हेतू , पार्ट में आवश्यक हों वहाँ मजबूती बढ़ाने हेतू , नुकीली edges को छिपाने हेतू , projection वेल्डिंग में उपयुक्त उभरी रचनाएं (dimples) बनाने हेतू , और पार्ट की location (स्थान निर्धारण) में उपयुक्त हो ऐसी रचनाएं (detail) बनाने हेतू forming ऑपरेशन किया जाता हैं.
Forming ऑपरेशन में सूक्ष्म स्तर पर material की अंदरूनी संरचना दबाव (compression) और खिंचाव (tension) से प्रभावित हो कर स्थानांतरित होती रहती हैं. इसे प्रेस technology की भाषा में मेटल फ़्लो (metal flow) कहा जाता हैं. अपितु flow याने बहना यह शब्द साधारणतया तरल एवं गैस के रूप में जो पदार्थ हैं उनके लिए इस्तेमाल होता हैं.
Bending की अपेक्षा forming में मेटल फ़्लो अधिक अनियमित एवं अप्रत्याशित (non-uniform, irregular , uneven) होता हैं. Forming ऑपरेशन सरल भी हो सकते हैं और अत्यधिक जटिल भी हो सकते हैं. Forming में सपाट blank का सटीक निर्धारण (blank development) करना बहुत चुनौतीपूर्ण होता हैं और इसमें उच्च स्तर के कौशल्य की आवश्यकता रहती हैं. निम्न उदाहरण से यह स्पष्ट होता हैं. यह टॉर्च के बटन की assembly का पार्ट हैं जो मैंने वर्ष 2005 में बनाया था.
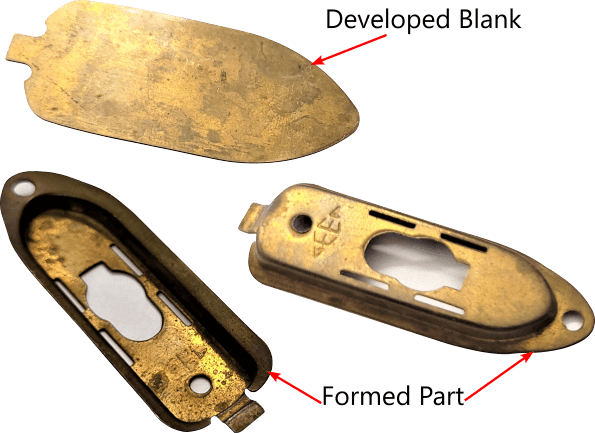
इसकी चार ट्रायल के बाद पाँचवी blank लगभग 90 प्रतिशत ‘सही’ बनी थी. customer की स्वीकृति की वजह से 90 प्रतिशत पर ही इस blank को final माना गया था. इसमें बहुत समय, कौशल और मेहनत लगती हैं. इसे टालने की युक्ति भी हैं. एक आयताकार blank बना ली होती जो मोटामाटी सही साइज़ की होती. Forming के बाद अतिरिक्त मटीरीअल trimming डाई का इस्तेमाल करते हुए पार्ट से अलग कर ली जाती. यह बहुत आसान रहता परन्तु एक अतिरिक्त ऑपरेशन (trimming), एक अतिरिक्त डाई और प्रत्येक पार्ट में कुछ अतिरिक्त मटीरीअल छोड़ रखना पड़ता. इसके चलते लागत और खर्च दोनों ही बढ़ जाते.
Forming ऑपरेशन के मोटे तौर पर निम्न पाँच प्रकार हैं:
- Embossing
- Coining
- Curling
- Bulging
- Restriking
Embossing ऑपरेशन
Embossing ऑपरेशन forming ऑपरेशन का वह प्रकार हैं जिसमें forming बहुत सीमित जगह (area) पर एवं बहुत कम गहराई तक ही की जाती हैं. Dimples (छोटे गड्ढे details) एवं रिब्स (ribs) इसके बहुत आम उदाहरण हैं.
पतली शीट में बड़ी dimple emboss करते हैं तब शीट के खिंचाव की वजह से होने वाली thinning (पतला होना) बहुत कम रहती हैं (नीचे बाएं) . जबकि मोटी शीट में की हुई छोटी dimple बनते समय thinning ज्यादा होती हैं. (नीचे दाएं)
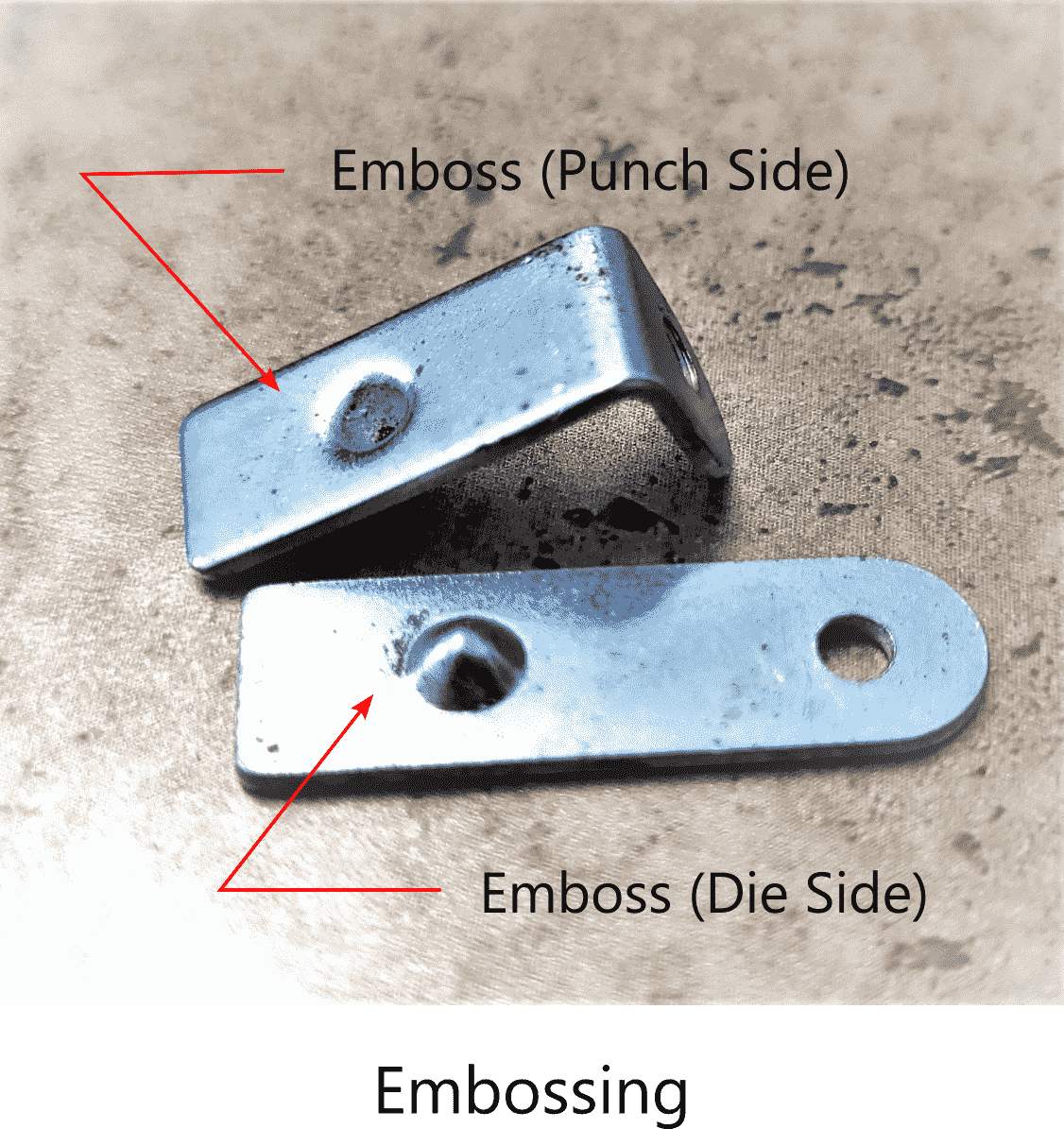
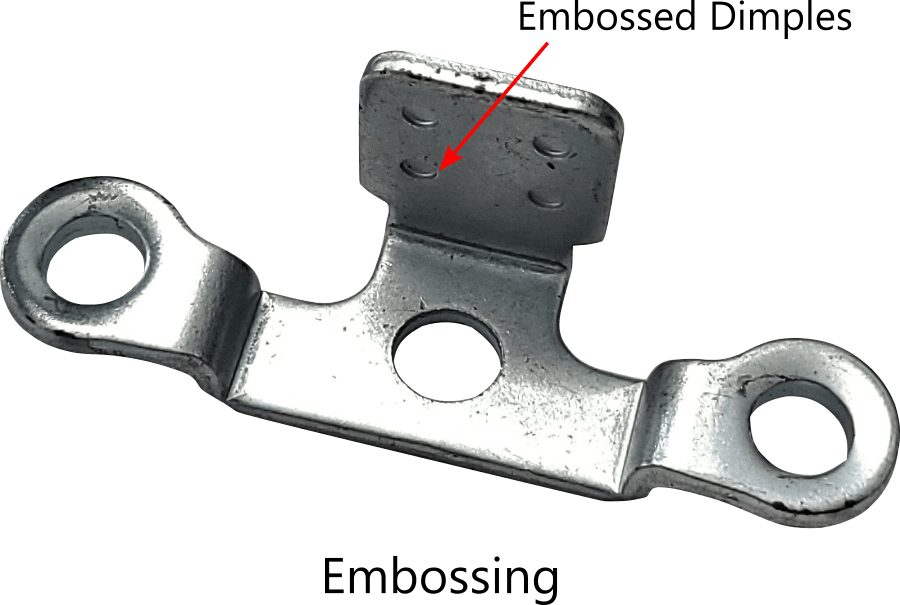
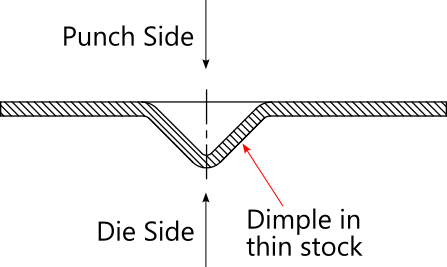
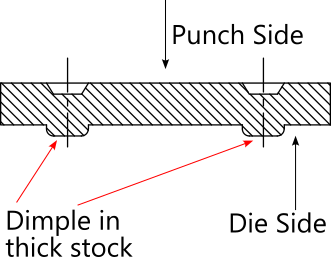
पतली सतह को मजबूती एवं समतलता प्रदान करने वाली embossing बर्तनों के ढक्कन एवं पेंदे में अक्सर पाई जाती हैं.
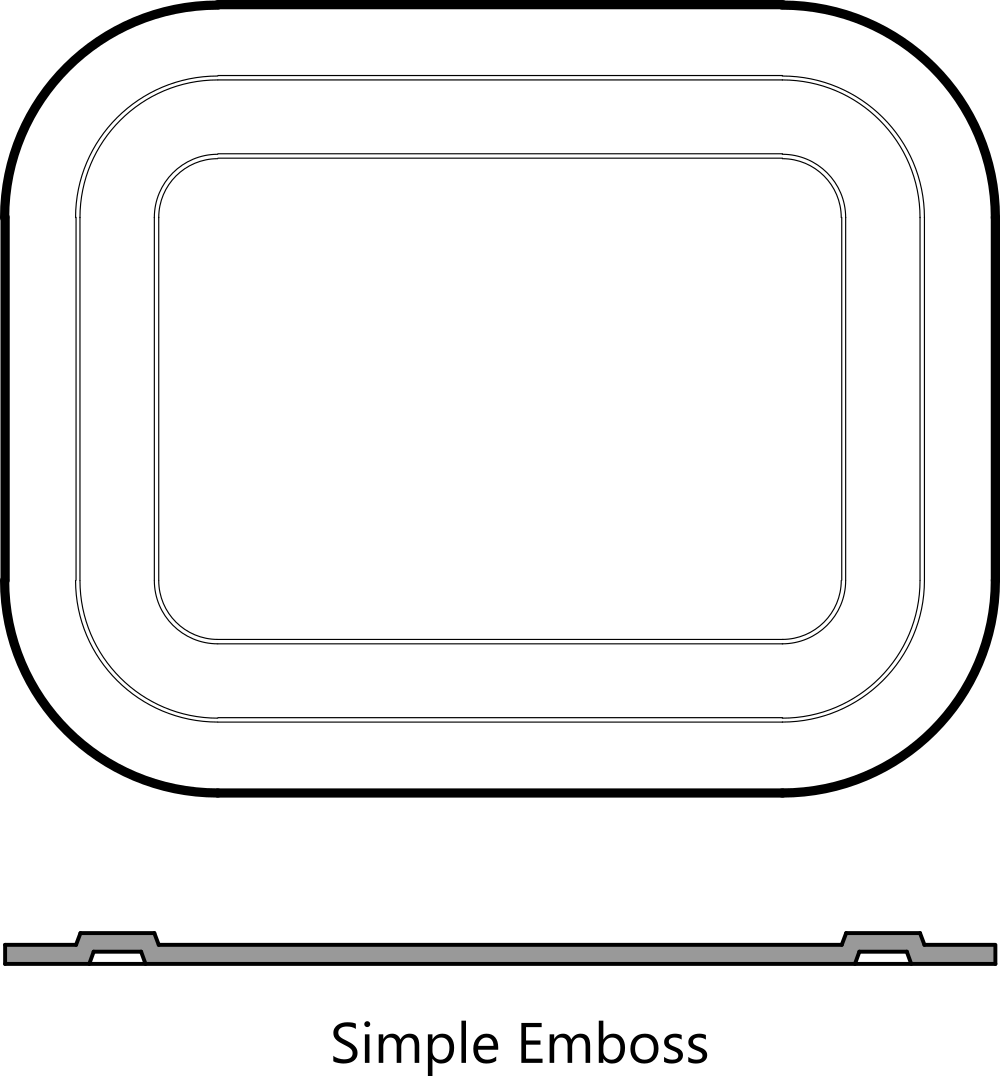
एक और प्रकार की embossed रचना जो बहुत आम तौर पर विशेष रूप से bending वाले कम्पोनन्ट में पाई जाती हैं वह हैं Gusset Emboss जो नीचे आकृति में दिखाई हैं. यह Rib (रिब) भी कहलाती हैं. उद्देश्य होता हैं की bend ‘खुल’ न जाए. इसलिए Gusset रचना bending लाईन पर ही की जाती हैं.
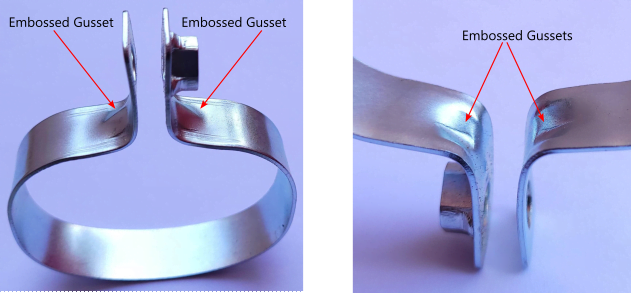
बेन्डिंग लाईन पर एमबोस किए गए रिब
Coca Cola एवं उस जैसे अन्य पेयों के एल्युमिनियम के can के गोलाकार पेंदे थोड़े अंदर की ओर धँसे होते हैं. ये embossing ऑपरेशन से बनाएं जाते हैं. भीतर की गैस के प्रेशर से इनके पतले पेंदे बाहर की ओर फूल न जाएं इस कारण ऐसे emboss किए जाते हैं. इन concave emboss की वजह से पेंदों की ताकत (strength) बढ़ती हैं.
Coining ऑपरेशन
Coining एक ऐसा press ऑपरेशन हैं जिसमें मेटल अति उच्च दबाव पर डाई के भीतर दबाया जाता हैं जिससे डाई के अंदरूनी सतह पर जो बहुत छोटी छोटी रचनाएं (detail) बनी होती हैं उसनें मेटल धँस जाता हैं और वे सारे detail पार्ट की सतह पर उभर आते हैं.
मुद्रा एवं सिक्के Coining ऑपरेशन से बनाए जाते हैं. पारंपरिक रूप से रसोई में इस्तेमाल होने वाले चम्मच एवं फोर्क (spoons and forks) के हैन्डल पर भी coining ऑपरेशन द्वारा सजावटी डिजाइन बनाएं जाते रहें हैं.
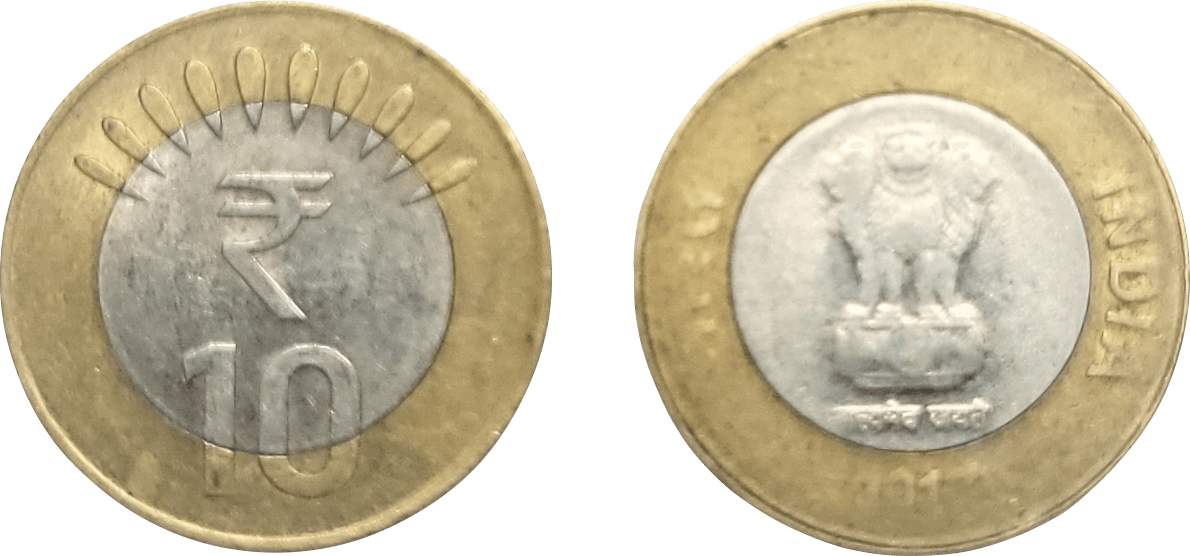
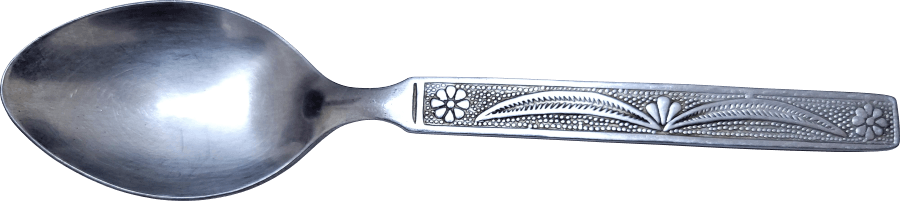
Coining ऑपरेशन का जिक्र कभीकभी ‘cold forming’ एवं ‘cold forging’ जैसे वैकल्पिक शब्दों द्वारा भी किया जाता हैं. ये इसलिए क्यों की coining और forging में कई समानताएं हैं.
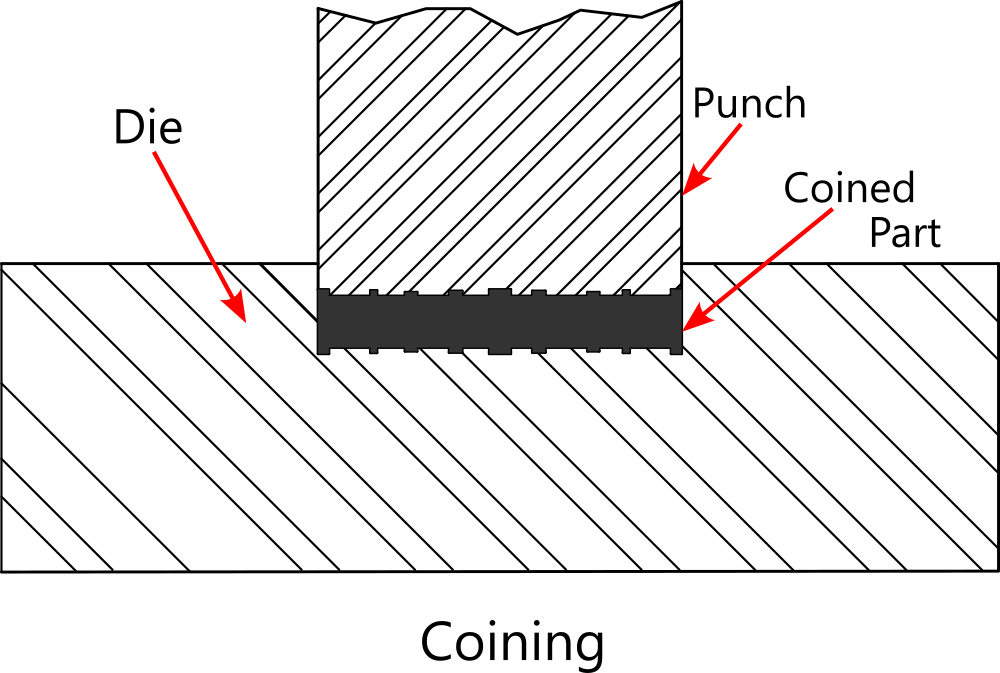
Embossing और Coining में क्या फर्क हैं?
Embossing में पार्ट की एक सतह पर detail उभरा हुआ होता हैं तो दूसरी सतह पर यही detail अंदर धँसा हुआ होता हैं जैसे की निम्न आकृति में बाईं ओर दिखाया हैं. Coining में एक सतह पर detail उभरा हुआ तो होता हैं परन्तु दूसरी सतह सपाट या उभरी हुई हो सकती हैं , यानि की detail में स्थानीय ‘thickening’ पाईं जाती हैं (मोटाई में स्थानीय बढ़ोतरी). Coining ऑपरेशन में कुछ जगह thinning (पतला होना) तो कुछ जगह thickening पाई जाती हैं. Embossing में मोटाई में कोई विशेष बड़ा बदलाव नहीं आता.
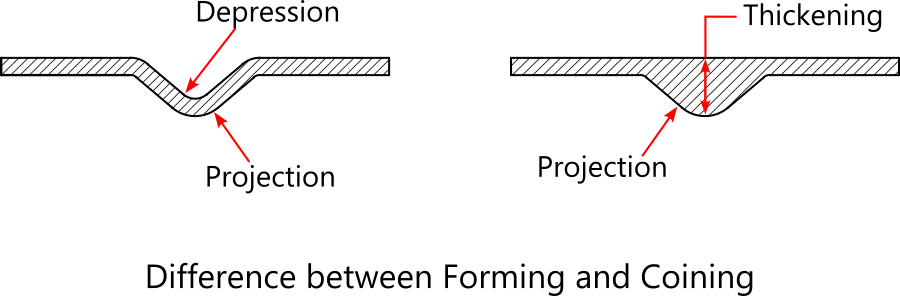
Curling ऑपरेशन
Curling ऑपरेशन वो हैं जिसमें ड्रॉ किए हुए पार्ट के किनारों को forming द्वारा गोल मोड़ा जाता हैं. ड्रॉ के पश्चात किनारे धारदार और खुरदरे होते हैं. इनसे त्वचा कटने की संभावना रहती हैं. Curling वाले किनारे सुरक्षित होते हैं. साथ ही ये किनारे सुंदरता एवं मजबूती भी प्रदान करते हैं.
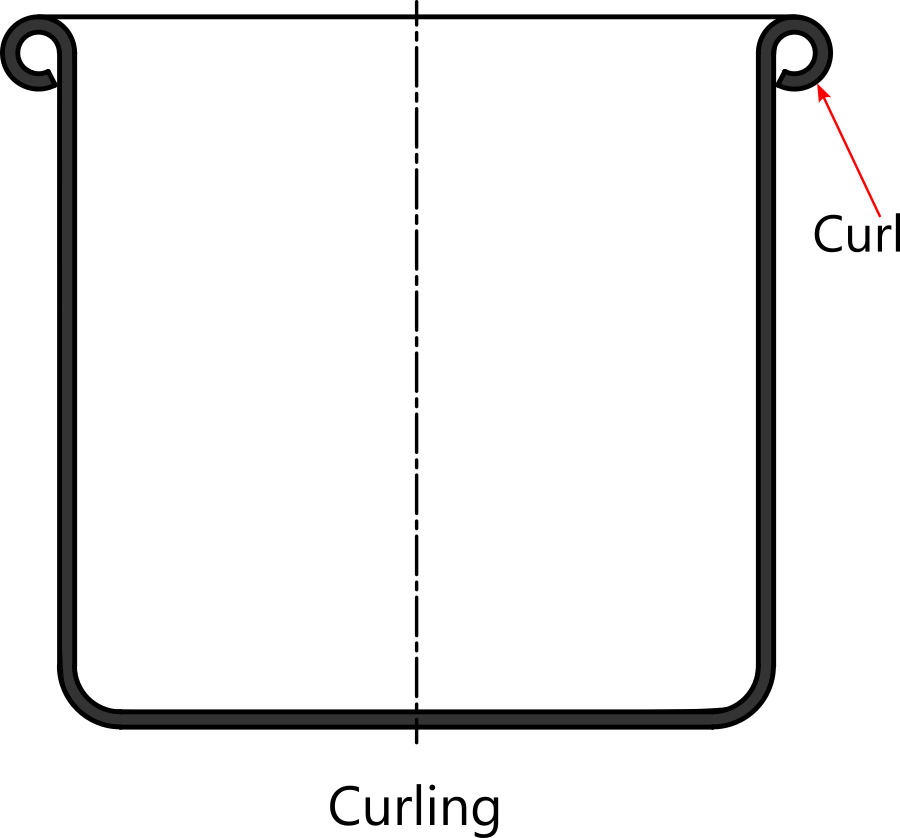
पतले किनारे curling द्वारा नजदीक से (छोटी radius में) मोड़ने में अधिक सुविधा रहती हैं. Curling ज्यादातर उन पार्ट्स में पाई जाती हैं जिन्हें हाथों से handling करने की आवश्यकता रहती हैं जैसे की रसोई में इस्तेमाल होने वाले बर्तन.
Bulging ऑपरेशन
Bulging ऑपरेशन ऐसा प्रेस ऑपरेशन हैं जिसमें ड्रॉ किए हुए कपनुमा पार्ट की भीतरी सतह पर दबाव डाल कर उसे बाहर की ओर फुलाया जाता हैं. पाईप एवं ट्यूब पर भी Bulging अक्सर किया जाता है. Bulging ऑपरेशन सुंदरता बढ़ाने हेतू एवं assembly करने हेतू किया जाता हैं.
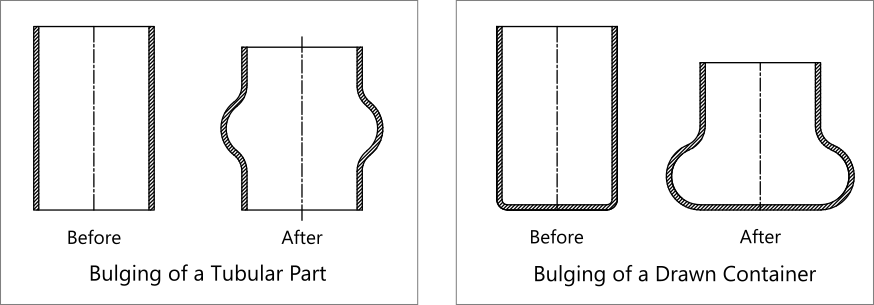
Restriking ऑपरेशन
Restriking एक दोय्यम प्रेस ऑपरेशन हैं जिसमे draw किए हुए पार्ट के पेंदे पर स्थित बड़ी radius को छोटी बनाने हेतू छोटी radius वाले पंच से पुन: प्रेस किया जाता हैं और radius के सिवा कहीं कोई बदलाव नहीं आता.
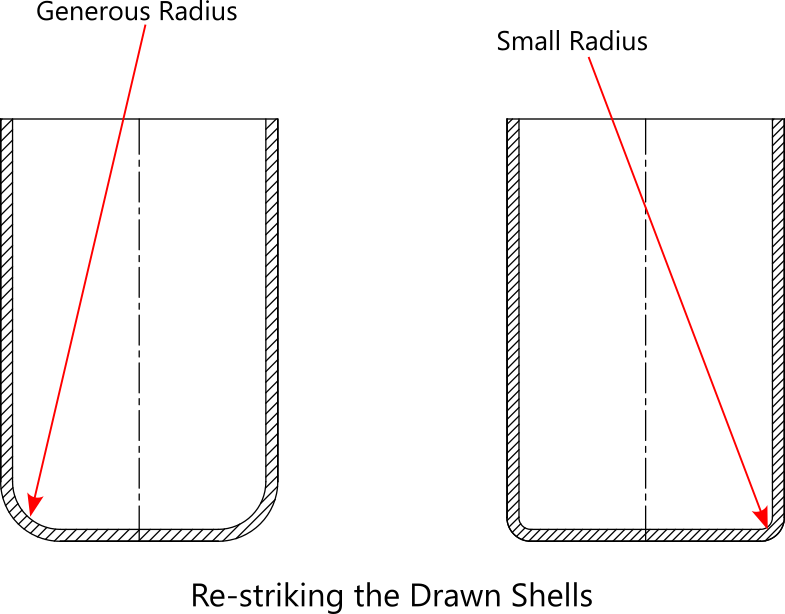
ड्रॉ ऑपरेशन की एक मर्यादा यह हैं की पेंदे के कोने वाली radius एक सीमा से छोटी रखने पर draw ऑपरेशन के दौरान पार्ट फट जाता हैं और draw विफल हो जाता हैं. Draw सफल करने हेतू radius का बड़ा होना अनिवार्य हो जाता हैं. परन्तु यह पार्ट ड्रॉइंग के अनुसार अस्वीकार्य होने की वजह से radius को छोटी करना आवश्यक हो जाता हैं. इसके चलते restriking एक अतिरिक्त दोय्यम ऑपरेशन के रूप में करना पड़ता हैं.
Drawing ऑपरेशन
Drawing एक ऐसा प्रेस ऑपरेशन हैं जिसमें मेटल फ़्लो इस तरह से नियंत्रित किया जाता हैं की फ्लैट blank कप , बर्तन , बोतल जैसे पात्र में परिवर्तित हो जाते हैं.
Blank के आकार एवं दिखावट में भले ही बहुत अधिक बदलाव दिखाई देते हों परन्तु blank का surface area और पात्र के surface area में कोई भारी बदलाव नहीं आते. क्योंकि surface area कायम रहता हैं तो स्वाभाविक हैं की दोनों का वजन भी कायम रहता हैं.
कोई भी प्रेस ऑपरेशन डाई designer एवं डाई maker के लिए उतना चुनौतीपूर्ण नहीं हैं जितना की draw ऑपरेशन. इस ऑपरेशन को सफल बनाने के लिए डाई designer एवं डाई maker के पास उच्च कोटी का कौशल एवं अनुभव होना बहुत जरूरी होता हैं.
गोलाकार पात्र का draw ऑपरेशन उतना जटिल नहीं होता जितना की चौरस और आयताकार पात्र का होता हैं. इसकी वजह यह हैं की गोलाकार पात्र की blank गोलाकार होती हैं जिसमें सभी दिशा में मेटल फ़्लो बाहर से केंद्र की ओर नियमित होता हैं. अन्य आकारों में केंद्र से अंतर की भिन्नता की वजह से मेटल फ़्लो सभी दिशाओं में अप्रत्याशित और अनियमित होता हैं. अन्य आकारों की draw ऑपरेशन में बहुत कौशल की आवश्यकता रहती हैं. Draw ऑपरेशन में सफलता पाने हेतू Draw Quality Steel का इस्तेमाल किया जाना चाहिए क्योंकि उसमें जो लचीलापन होता हैं वो सभी दिशाओं में एकसमान होता हैं.
Draw ऑपरेशन के कई प्रकार हैं जैसे की
- Shallow drawing (उथला drawing)
- Deep drawing (गहरा drawing)
- Redrawing (पुन: draw करना)
- Ironing (आयरनिंग)
- Collar drawing (कॉलर drawing)
मैंने जिन deep drawing पार्ट्स की डाइयाँ बनाई हैं वे पार्ट नीचे वाली तस्वीरों में दिखाई हैं.
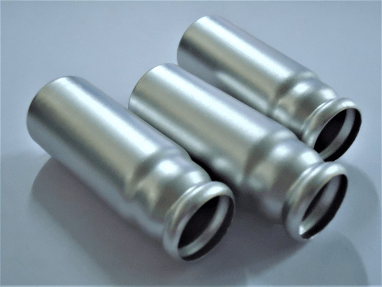
Spray Containers
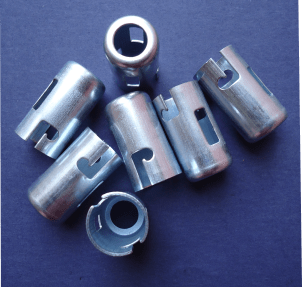
Automotive Bulb Holders
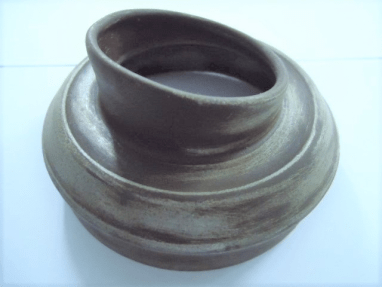
Silencer End Cap
Shallow Drawing ऑपरेशन
Shallow (उथला) Drawing वो प्रेस ऑपरेशन हैं जिसमें draw की height पात्र के diameter के 50 प्रतिशत से अधिक नहीं होती.
यदि diameter 50 mm और height 25 mm या उससे कम हैं तो वो shallow ड्रॉ कहलाएगा. गणितीय अनुपात की भाषा में इसका मतलब हैं की height बटा diameter (h/d) अनुपात 0.5 से नीचे हो तो shallow ड्रॉ और ऊपर हो तो deep draw कहा जाएगा. अनुपात के 0.5 से अधिक होने पर एक से अधिक बार draw करने होंगे.
नीचे दी गई आकृति में , बाईं ओर shallow draw और दाईं ओर deep draw दर्शाया हैं.
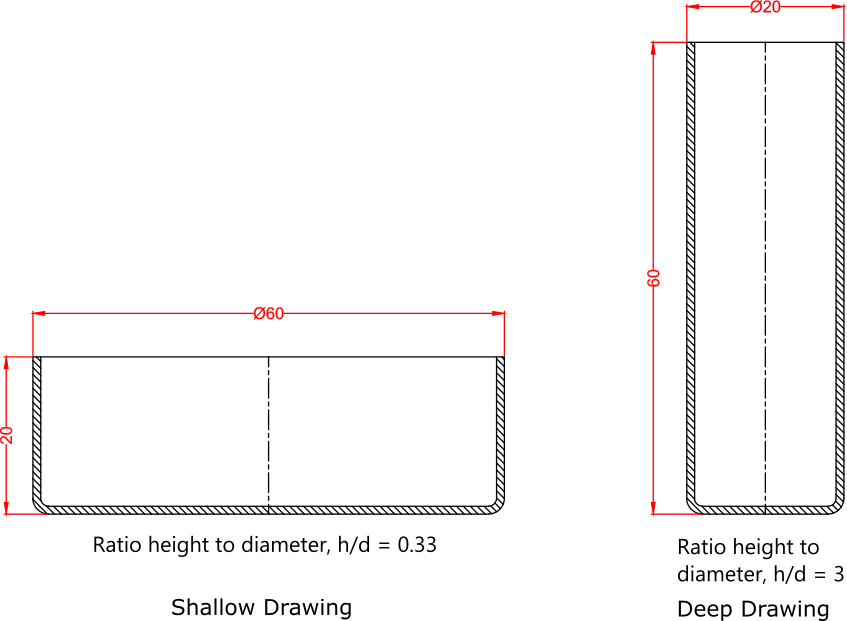
Deep drawing की अपेक्षा shallow drawing सरल और सुगम होती हैं. इसकी वजह ये हैं की deep drawing प्रक्रिया में मेटल फ़्लो बहुत अधिक जटिल होता हैं. Deep drawing डाई की design और डाई बनाने में अपेक्षाकृत अधिक समय , ट्रायल , अनुभव और कौशल की आवश्यकता रहती हैं.
आम तौर पर डिब्बों में ढक्कन shallow ड्रॉ द्वारा और डिब्बे deep ड्रॉ द्वारा बनाए पाएं जाते हैं.
Deep Drawing ऑपरेशन
Drawing ऑपरेशन का एक बहुत शानदार एवं महत्वपूर्ण प्रकार हैं Deep Drawing जिसमें अधिक गहरे पात्र अनेक चरणों में draw कर के बनाए जाते हैं.
प्रेस ऑपरेशन में deep drawing से अधिक जटिल प्रकार शायद ही कोई हों. ड्रॉ के प्रत्येक अगले चरण में पिछले चरण की अपेक्षा diameter कम की जाती हैं और गहराई (height) बढ़ाई जाती हैं. जब h/d अनुपात 0.5 से अधिक बैठता हैं तब स्वाभाविक हैं की एक ही ड्रॉ में पार्ट न बनेगा – फट जाएगा. तब deep drawing ऑपरेशन की सहायता लेनी होगी.
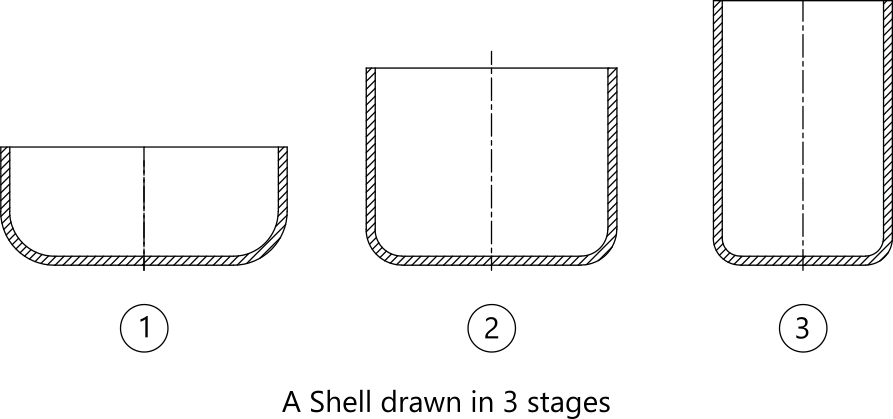
Deep ड्रॉ में मेटल कैसे एक आकार से दूसरे आकार में परिवर्तित होता हैं यह समझने के लिए एक उदाहरण लेते हैं. नीचे की आकृति में एक drawing से बना कप दिखाया हैं. शीट की thickness 1 mm हैं. ऐसी कल्पना कर सकते हैं की कप का आकार A, B और C इन तीन विभिन्न आकारों का संयोजन हैं. A यानि पेंदे में जो फ्लैट डिस्क जैसा हिस्सा है वह. B यानि पेंदे को ऊपर वाले बड़े हिस्से से जोड़ने वाला radius वाला घुमावदार हिस्सा. C यानि सबसे ऊपर वाला बड़ा पाईपनुमा हिस्सा.
यह तो सामान्य बुद्धि से भी स्पष्ट होता हैं की , Blank का वजन = Draw वाले पार्ट का वजन. यदि thinning (thickness कम होना , पतला हो जाना) नहीं होता तो Blank का वजन = Draw वाले पार्ट का वजन का मतलब होगा
Blank का surface area = Part का surface area = Area (A+B+C)
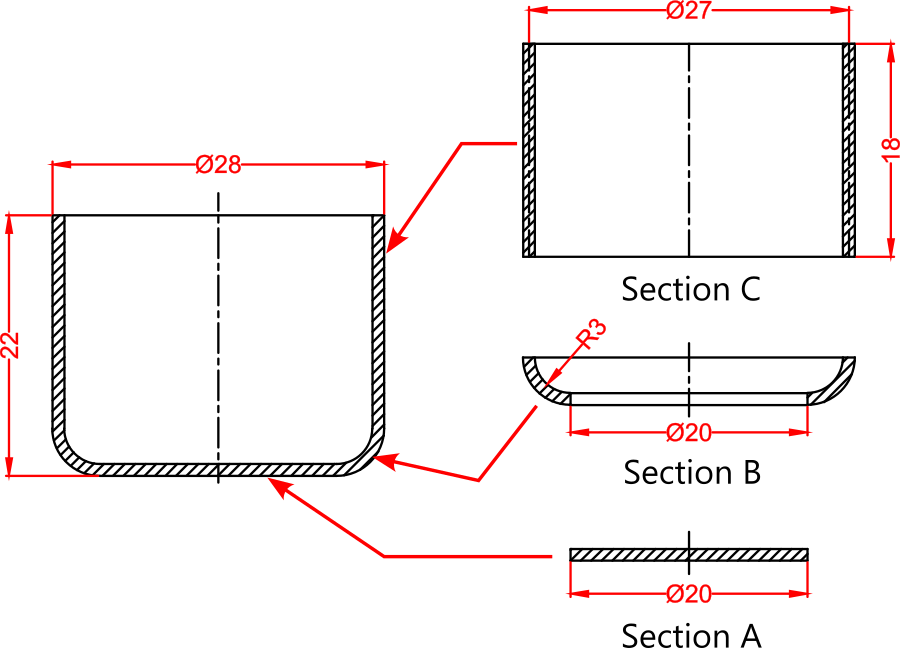
नीचे वाली आकृति में area A, B और C दिखाएं हैं. पेंदे का आकार जैसे था वैसा ही रहेगा, कोई बदलाव न होगा. यह याद रखने वाली बात हैं की ड्रॉ के पश्चात पेंदे का आकार अपरिवर्तित रहता हैं. यह आकार केंद्र (center) में रहेगा यह स्वाभाविक हैं. इस पेंदे के इर्दगिर्द एक रिंगनुमा आकार में material चाहिए होगा जिसका surface area B जितना होना चाहिए. यह रिंग पेंदे से जुड़ी होगी. आखिर में एक और रिंग जोड़नी होगी जिसका surface area C जितना होगा और जिससे पाईपनुमा हिस्सा बनेगा. तो इस प्रकार blank की साईज़ निर्धारित करी जाती हैं.
यह blank, drawing डाई पर रखी जाएगी. सेंटर सुनिश्चित करने हेतू blank के इर्दगिर्द एक locator रहेगा. जब पंच नीचे आएगा तो पहले blank को स्पर्श करेगा. अधिक नीचे जाने पर पेंदे के हिस्से में material हैं उसके सिवा सारा बाहरी material डाई के सेंटर की ओर खिसकने लगेगा (metal flow). पेंदे के सर्कल से सटा बाहरी मटीरीअल भीतर की ओर खिसकते समय उस पर कम compressive दबाव रहेगा जबकी पेंदे से सुदूर जो material हैं उसे अधिक compressive दबाव झेलना पड़ेगा. उस मटीरीअल के सारे बिन्दु एकदूसरे के नज़दीक आएंगे जिससे की वहाँ thickening (मोटाई बढ़ना) वाली परिस्थितियाँ बनेगी. ऐसी परिस्थितियाँ जब काबू में नहीं रहती तब material के उन हिस्सों में लहरें (wrinkles, रिंकल्स) बन जाती हैं और ड्रॉ विफल हो जाता हैं. इसका मतलब यह हैं की सुदूर material पेंदे से जीतने कम अंतर पर होगा उतनी draw की सफलता की संभावना बढ़ जाएगी. यही होता हैं जब किसी draw को दो , तीन, चार या अधिक चरणों में किया जाता हैं. हर चरण में सुदूर material पेंदे से कम दूरी पर हों यह सुनिश्चित किया जाता हैं.
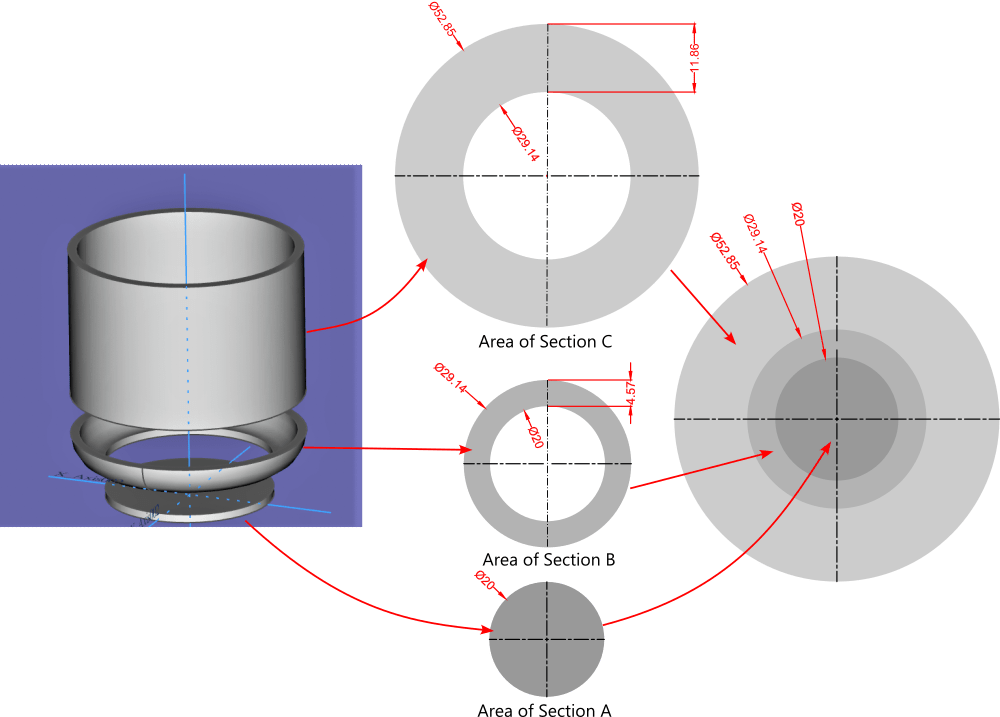
Redrawing ऑपरेशन
पहले से draw किए हुए पार्ट्स को कम clearance वाली डाई में जब फिरसे draw करते हैं तो उस ऑपरेशन को redraw कहतें हैं. Draw की दीवारें सीधी करने हेतू एवं बहुत सटीक dimension पाने हेतू redraw का प्रयोग होता हैं.
यह सर्वविदित हैं की किसी भी draw में सफलता प्राप्त करने हेतू draw डाई एवं पंच के बीच thickness से 5-15 प्रतिशत तक अधिक क्लियरन्स रखा जाता हैं. इस कारण draw किए हुए पार्ट में कुछ न कुछ मात्रा में taper होता ही हैं जो नीचे की आकृति में दिखाया गया हैं. इसके परिणामस्वरूप पार्ट की top diameter और पेंदे के diameter में फर्क आ जाता हैं. जब यह स्वीकार्य न हों तब इस taper से निज़ात पाना आवश्यक हो जाता हैं. ऐसी परिस्थितियों में एक दूसरी डाई में thickness से 0.02 mm – 0.04 mm कम clearance रखते हुए पुन: draw किया जाता हैं.
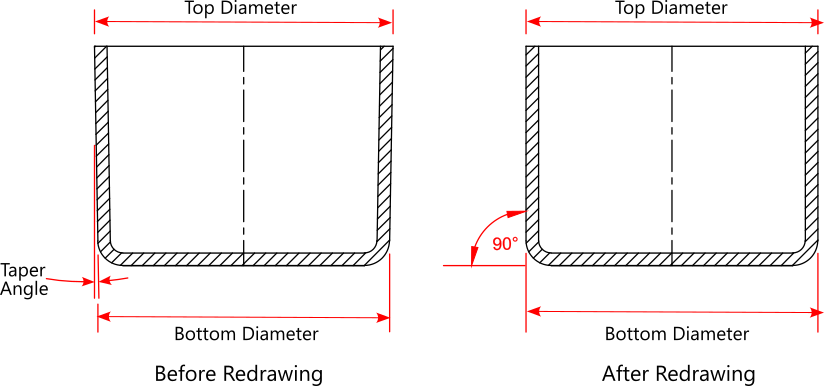
Redrawing ऑपरेशन से पार्ट की taper दीवारें सीधी तो हो जाती ही हैं, अपितु बाहरी finish में भी उल्लेखनीय सुधार आता हैं.
Ironing ऑपरेशन
Ironing (आएरनिंग) ऑपरेशन Drawing ऑपरेशन का ऐसा प्रकार हैं जिसमें पहले ही draw किया हुआ पार्ट फिर से बहुत टाइट क्लियरन्स वाली डाई में ड्रॉ कर के पार्ट की thickness बाहर से कम की जाती हैं.
नीचे दी गई आकृति से स्पष्ट होता हैं की thickness बाहर से कम होती हैं यानि की पार्ट का बाहरी diameter पहले से तनिक छोटा हो जाता हैं जबकी भीतर का diameter बदलता नहीं हैं.
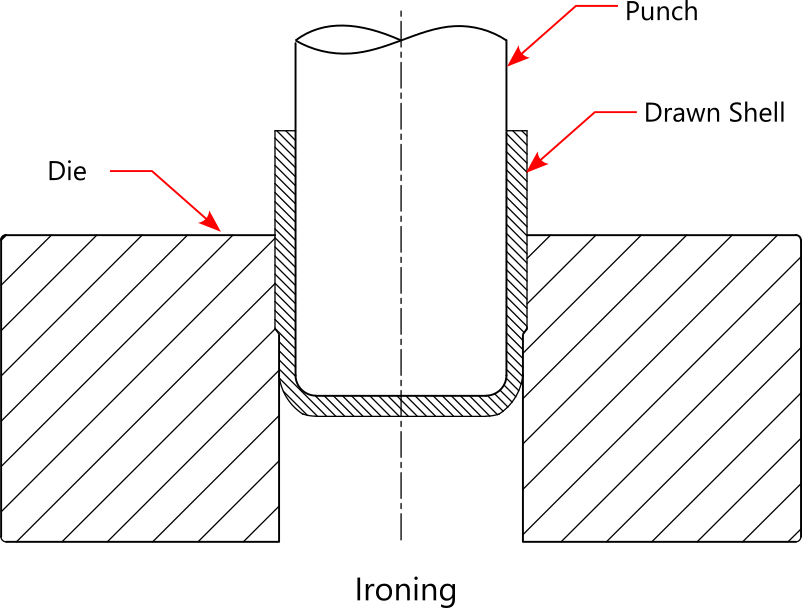
पार्ट के बाहरी (outer) diameter से थोड़े छोटे diameter वाली draw डाई में पार्ट को पुन: ड्रॉ किया जाता हैं, जबकी पंच का diameter पार्ट के अंदरूनी diameter जितना ही रखा जाता हैं. इससे होता यह हैं की पार्ट के बाहरी diameter पर दिया हुआ टालरन्स (tolerance) प्राप्त हो जाता हैं जो की पारंपरिक ड्रॉ में मुश्किल हैं. हालाँकि , ironing ऑपरेशन में पार्ट की height में छोटी सी वृद्धि जरूर होती हैं. साथ ही पार्ट की बाहरी finish में उल्लेखनीय वृद्धि होती हैं.
Collar Drawing ऑपरेशन
Collar drawing ऐसा ऑपरेशन हैं जिसमें पहले से piercing किए हुए छेद (hole) के आस-पास का material केंद्र से बाहर की ओर खींच कर draw करते हुए collar बनाया जाता हैं जैसे की नीचे की दोनों तस्वीरों में दिखाया गया हैं.
अन्य ड्रॉइंग ऑपरेशन से collar ड्रॉइंग भिन्न हैं वो ऐसे:
- Material बाहरी हिस्सों से केंद्र की ओर नहीं , बल्के केंद्र से बाहर की ओर खिसकता (फ़्लो) हैं.
- Material की आंतरिक संरचना tension में रहती हैं.
- छेद (hole) का होना आवश्यक हैं.
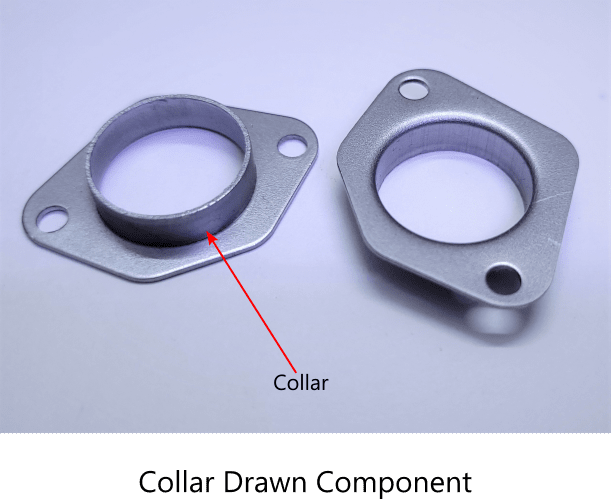

इन विशेषताओं के कारण इस ऑपरेशन में thinning ही होता हैं , thickening कभी नहीं होता जिसके फलस्वरूप collar फटने की ही संभावना बनी रहती हैं , wrinkling की नहीं. जितनी collar height ज़्यादा उतनी ही फटने की संभावना ज़्यादा रहती हैं.

Collar drawing का उद्देश्य क्या हैं?
छेद के आस-पास height बढ़ाना collar drawing ऑपरेशन का मुख्य उद्देश्य होता हैं. परंतु height बढ़ाने की आवश्यकता क्यों पड़ती हैं? वो इसलिए की असेम्बली (assembly) हेतू यदि स्क्रू कसने के लिए चूड़ियाँ बनानी हों तो hole के आस-पास height ज़्यादा होनी चाहियें. ऐसें उद्देश्यों की पूर्ति के लिए मोटी शीट से बने पार्ट्स के छेद पर collar draw करना अधिक फायदेमंद रहता हैं, जैसे की निम्न तस्वीरों में दिखाया गया हैं.
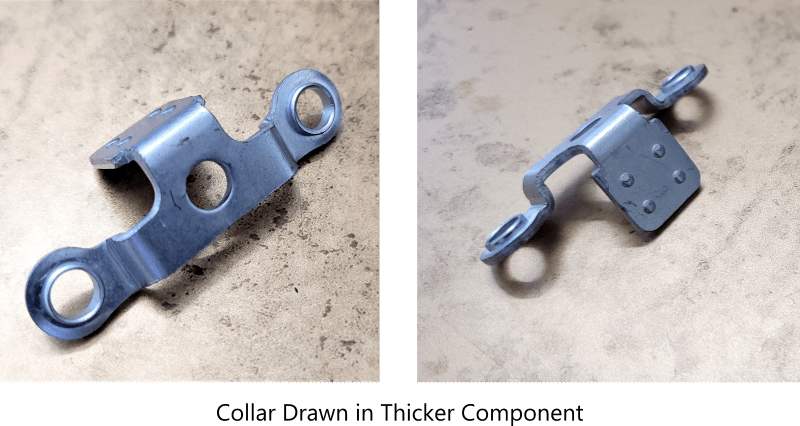
कभी कभी दो पार्ट को प्रेस फिट करने की आवश्यकता पड़ती हैं. तब hole के आस-पास की collar का प्रयोग assembly अधिक पक्की एवं मज़बूत करने के लिए हो सकता हैं. यह नीचे की तस्वीर में देखा जा सकता हैं.
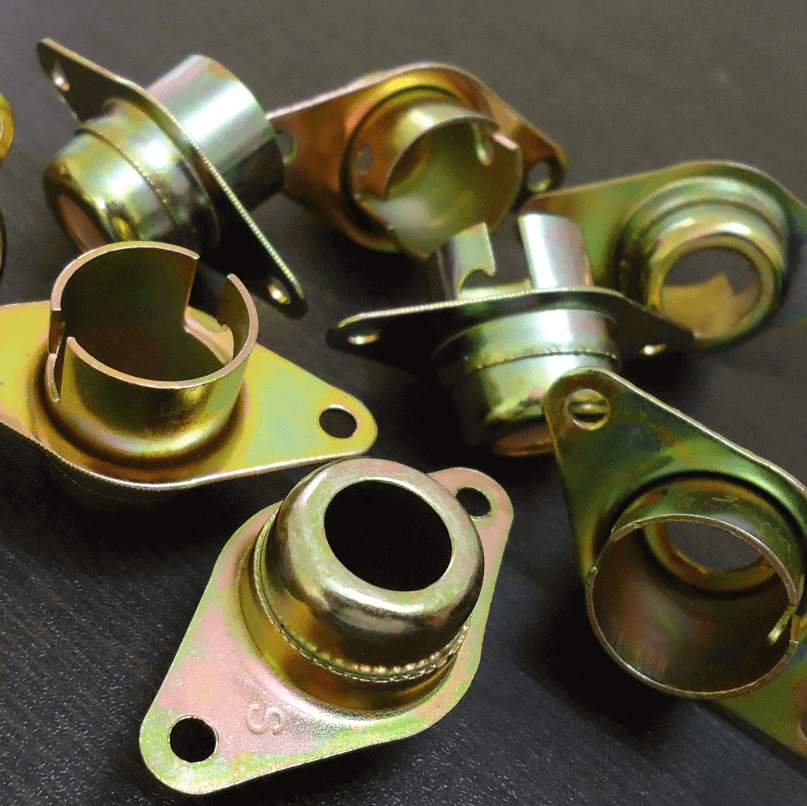
Press fit assemblies using drawn collar
शीट मेटल प्रेसींग प्रक्रिया की मर्यादाएं क्या हैं ?
अन्य manufacturing प्रक्रियाओं की तरह शीट मेटल प्रेसींग प्रक्रिया की भी कुछ मर्यादाएं हैं वे निम्न प्रकारकी हैं :
- क्योंकि प्रेस पार्ट शीट से बने होते हैं और शीट एकसमान मोटी होती है , पार्ट भी एकसमान मोटाई के बनते हैं . मोटाई में भिन्नता प्राप्त करना सम्भव नहीं हैं . कई बार पार्ट्स के कुछ हिस्सों की ताकत बढ़ाने हेतू मोटाई बढ़ाना जरूरी होता है.
- मोटे पार्ट्स की bending में छोटी bend radius रखने पर काफी मर्यादाएं होती हैं
- प्रेस पार्ट्स के किनारे खुरदरे होते हैं . किनारों की quality निम्न स्तर की होती हैं
- बहुत छोटे एवं बहुत बड़े पार्ट्स बनाने हेतू यह प्रक्रिया अव्यावहारिक हैं
- यह प्रक्रिया मुलायम एवं नमनीय (soft and ductile) मटीरीअल के लिए श्रेष्ठ हैं परन्तु जहाँ हाई strength की आवश्यकता होती हैं वहाँ हार्ड मटीरीअल इस्तेमाल करना होता हैं, तब डाई क्रैक होकर टूटने का जोखिम बना रहता हैं.
- प्रेस मशीन और डाईयाँ महंगी होती हैं
- पार्ट्स में बदलाव करना हो तो डाईयोंमें भी उसके अनुसार बदलाव करने पड़ते हैं जो की महंगे भी हो सकते हैं और ज्यादा समय भी लग जाता हैं
- डाईयाँ विकसित करने में बहुत समय लगता हैं
- कम मात्रा में उत्पादन करने के लिए यह प्रोसेस उपयुक्त नहीं हैं क्योंकि तब ये किफायती नहीं रहती.
निष्कर्ष
manufacturing इंडस्ट्री में सबसे ज्यादा प्रयुक्त होने वाली प्रक्रिया हैं शीट मेटल प्रेसींग. जीवन के हर मोड पर प्रेस पार्ट्स मिल ही जाते हैं . उन इंडस्ट्रीज़ की यह पहली पसंदीदा manufacturing प्रक्रिया हैं जिन उद्योगों मे पार्ट्स की कम कीमते , बहुत हाई production और dimension की सटीकता में पुनरावृत्ति की बहुत दरकार होती हैं . ऐसी ही एक इंडस्ट्री हैं आटोमोबाईल इंडस्ट्री. शीट मेटल प्रेसींग के कई फायदे हैं परन्तु इसकी अपनी कुछ सीमाएं भी हैं .
Quiz -शीट मेटल प्रेसींग पर
आईए ,शीट मेटल प्रेसींग के विषय में आप क्या सीखें यह जानते हैं !